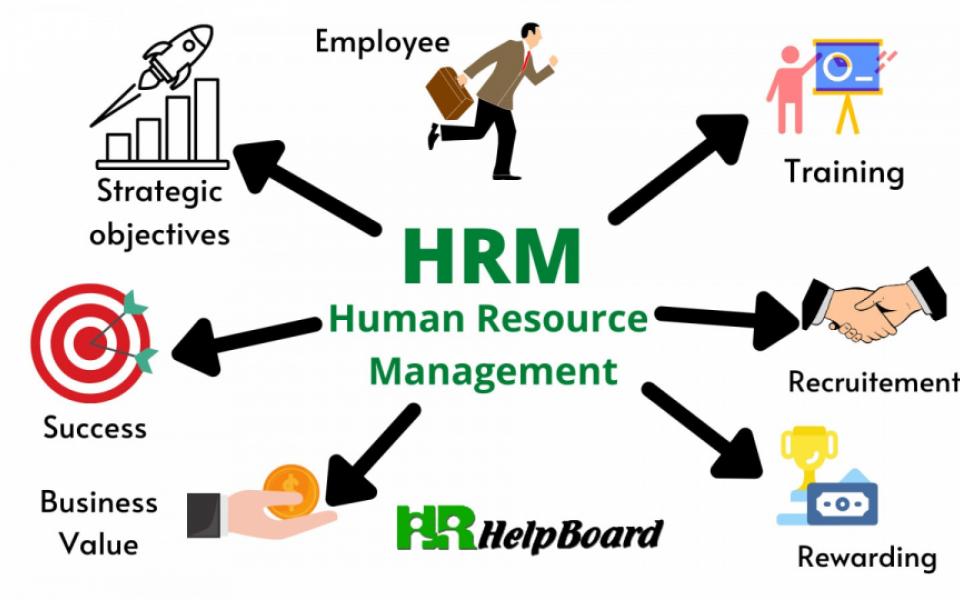
There are many things you need to keep in mind when dealing with construction debris. These include the types of waste, such as hazardous, recyclable, and off-site. There are also many regulations concerning the disposal and recycling of construction waste. This article will focus on hazardous waste, recycling, the importance to seperate hazardous waste from the remainder. When you are familiar with these areas, you will be able to make an informed decision about how to responsibly handle these materials.
Hazardous
You need special equipment and skills to dispose of hazardous materials. These wastes could cause serious harm to the community and the environment if they're not handled properly. In addition, improper disposal can lead to fines from the state authorities. Junk King is equipped to handle hazardous building waste. These are some of the most common construction wastes. These aren't all. Construction can present a danger to health and safety by producing hazardous waste. Here are some suggestions for how to manage construction waste.
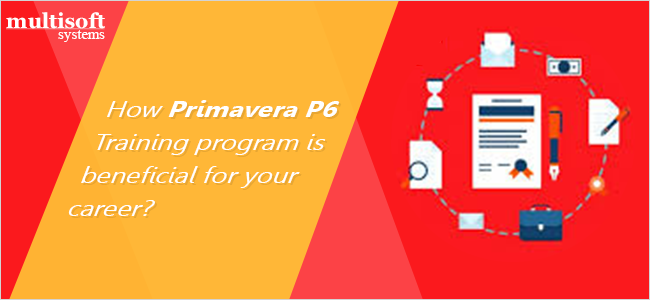
Trucks are used to transport construction and demolition debris to diversion centers. In the United States, the most common trucks are light and medium duty trucks. They have modular interoperability that allows them to be combined. Facility management plans specify what materials are acceptable for disposal, and refuse haulers may reject a load containing hazardous materials. The four characteristics associated with hazardous waste include corrosivity ignitability reactivity, toxicity, and reactivity. The Environment Agency (AE) and California Department of Environmental Quality, (CDEQ), have to manage hazardous waste.
Recyclable
It's important that you take action to reduce the amount construction waste that ends up in the landfills. California Green Building Standards Code requires that builders prepare a plan for managing construction waste before they can be approved and permitted. Materials you can recycle are: cardboard, metals (wood), insulation, ceiling tile and drywall; plastic, glass and plastic. Even composites such Hardplan siding, can be recycled.
Recycling construction waste has many advantages. Recycling construction waste has many benefits. It can help save energy and reduce the consumption of natural resources. You can save as much as one billion gallons annually by recycling all concrete and asphalt waste from construction projects across the US. Recycling your waste will also help the environment. It will reduce landfills' toxic waste and keep it out of waterways.
Off-site
Hong Kong Civil Engineering and Development Department owns two CWS facilities that can be used off-site. These facilities handled 5.11million tons of construction debris in February 2012. The program needs to be improved to achieve better results in the future. This paper examines the practices of the CWS program in Hong Kong and provides practical examples of how to improve the program. This will help construction professionals reduce their waste generation and minimize hauling costs. Contractors should tell suppliers to cut down on packaging to ensure a more efficient program for managing waste.
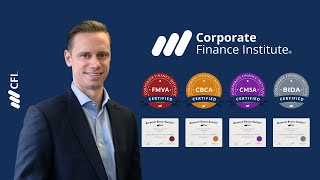
One advantage to disposing of construction waste off-site, is the ability quickly and easily identify the material. CWS that is off-site can be economically viable only if the materials are properly identified. Many contracting firms, subcontractors and project specifications include jobsite waste management protocols. Some building owners have established guidelines and corporate policies to guide construction waste disposal. Some service providers will even provide containers for materials. It is important to learn the legal requirements and the cost of disposal and recycling construction waste.
FAQ
How does a manager learn to manage?
It is important to have good management skills.
Managers need to monitor their subordinates' performance.
It is important to take immediate action if your subordinate doesn't perform as expected.
You must be able to spot what is lacking and how you can improve it.
What are the steps of the management decision-making process?
Managers have to make complex decisions. It involves many elements, including analysis, strategy. planning. implementation. measurement. evaluation. feedback.
It is important to remember that people are human beings, just like you. They make mistakes. You can always improve your performance, provided you are willing to make the effort.
This video shows you how management makes decisions. We will discuss the various types of decisions, and why they are so important. Every manager should be able to make them. These topics are covered in this course:
What kind of people use Six Sigma?
Six sigma is a common concept for people who have worked in statistics or operations research. It can be used by anyone in any business aspect.
It requires high levels of commitment and leadership skills to be successful.
How does a manager motivate their employees?
Motivation refers to the desire or need to succeed.
You can get motivated by doing something enjoyable.
You can also feel motivated by making a positive contribution to the success in the organization.
For example, if your goal is to become a physician, you will probably find it more motivational to see patients rather than to read a lot of medicine books.
The inner motivation is another type.
You may feel strongly that you are responsible to help others.
You might even enjoy the work.
If you feel unmotivated, ask yourself why.
Then, consider ways you could improve your motivation.
What role should a manager play within a company
Each industry has a different role for a manager.
A manager generally manages the day to-day operations in a company.
He/she will ensure that the company fulfills its financial obligations.
He/she makes sure that employees adhere to the rules and regulations as well as quality standards.
He/she plans and oversees marketing campaigns.
How does Six Sigma work?
Six Sigma uses statistical analysis to find problems, measure them, analyze root causes, correct problems, and learn from experience.
The first step is identifying the problem.
Next, data are collected and analyzed in order to identify patterns and trends.
The problem is then rectified.
Finally, data is reanalyzed to determine whether the problem has been eliminated.
This cycle continues until there is a solution.
What is Kaizen?
Kaizen refers to a Japanese term that stands for "continuous improvements." It is a philosophy which encourages employees in continuously improving their work environment.
Kaizen is founded on the belief of everyone being able to do their job well.
Statistics
- UpCounsel accepts only the top 5 percent of lawyers on its site. (upcounsel.com)
- The average salary for financial advisors in 2021 is around $60,000 per year, with the top 10% of the profession making more than $111,000 per year. (wgu.edu)
- Hire the top business lawyers and save up to 60% on legal fees (upcounsel.com)
- The BLS says that financial services jobs like banking are expected to grow 4% by 2030, about as fast as the national average. (wgu.edu)
- Your choice in Step 5 may very likely be the same or similar to the alternative you placed at the top of your list at the end of Step 4. (umassd.edu)
External Links
How To
How can you implement the Kaizen technique?
Kaizen means continuous improvement. The Japanese philosophy emphasizes small, incremental improvements to achieve continuous improvement. This term was created by Toyota Motor Corporation in 1950. It is a process where people come together to improve their processes.
Kaizen, a Lean Manufacturing method, is one of its most powerful. This concept requires employees to identify and solve problems during manufacturing before they become major issues. This is how you can improve the quality and lower the cost.
Kaizen is a way to raise awareness about what's happening around you. It is important to correct any problems immediately if they are discovered. If someone spots a problem while at work, they should immediately report it to their manager.
There are some basic principles that we follow when doing kaizen. The end product is always our starting point and we work toward the beginning. If we want to improve our factory for example, we start by fixing the machines that make the final product. Then, we fix the machines that produce components and then the ones that produce raw materials. Then we fix the workers, who directly work with these machines.
This is known as "kaizen", because it emphasizes improving each step. After we're done with the factory, it's time to go back and fix the problem.
How to measure kaizen's effectiveness in your business is essential to implement it. There are many ways to tell if kaizen is effective. One of these ways is to check the number of defects found on the finished products. Another way is to see how much productivity has increased since implementing kaizen.
Another way to know whether kaizen is working is to ask yourself why did you decide to implement kaizen. You were trying to save money or obey the law? You really believed it would make you successful?
Congratulations if you answered "yes" to any of the questions. You are ready to start kaizen.