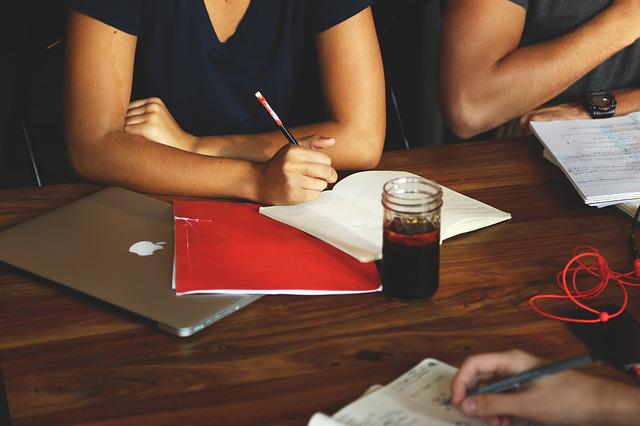
Management strategy is the process for defining and implementing key goals. It involves taking action on behalf all stakeholders. You should consider several important elements when developing a strategic plan. A management strategy must be specific and manageable. It is important that a strategy be executed in a coordinated way in order to reach its goals.
Strategies used to reach individual goals
In management, tactics are individual actions that contribute to a strategy. Tactics help you break down your strategy into tasks and due dates, allowing you to build a precise timeline. Tactics are specific tasks that make up a strategy. They make up the second half (or "how") of the "how-" category. Strategies define the project's goals, while tactics provide guidance on how to achieve those goals.
The organizational goals and the operational goals for a management team must be closely connected. These goals should be consistent with the organization's mission and vision. By doing this, employees will be able to identify the goals for which they are responsible. Goals are more likely when everyone works together.
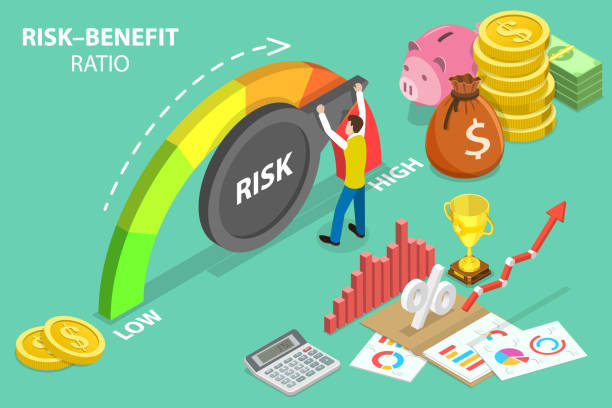
Tactics that are coordinated
Tactics are the activities carried out in a business to achieve goals and objectives. These include creating, delivering, and expanding value. By aligning its resources, tactics help businesses maintain their unique position in the market. These activities help to reinforce and support the strategy and ensure consistent customer service.
Both tactic and strategy originated in the military but were later adopted by businesses. A strategy is the overall plan to achieve a specific goal, and tactics are the specific steps and actions that are taken to accomplish the goal. Strategy is the long-term vision for the organization that defines the goal.
Organizational goals can be achieved using tactics
Tactics are actions taken to help achieve an organization's goals. These tactics are part and parcel of a strategic plan, which is a general blueprint that defines the company's future vision. These blueprints are made to work using tactics that integrate all resources. They can be used to reach a specific goal or be used as a cautionary measure in the event that the original strategy does not meet your expectations.
A tactic's effectiveness can be evaluated by assigning measurable numbers to it. For example, if an organization wants to hold more events, they can set a measurable number of events a year. You can also set a weekly or monthly limit on the number of events that are held each week. By assigning measurable values and tactics, it is possible to monitor their effectiveness and determine whether they are reaching company goals.
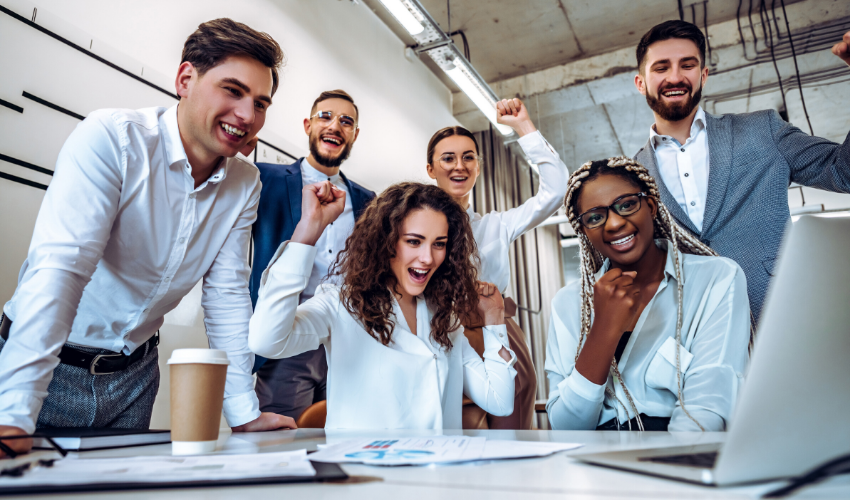
Next, identify the tactics that are most effective in achieving the goals. These tactics can be implemented quickly by a team and are easily actionable. These tactics are defined by managers, and can be evaluated using well-defined metrics. Furthermore, tactical plans often contain specific details regarding implementation and timelines.
FAQ
How does a manager learn to manage?
By practicing good management skills at all times.
Managers must monitor the performance of subordinates constantly.
You must act quickly if you notice that your subordinate isn’t performing to their standards.
You must be able to spot what is lacking and how you can improve it.
What are management concepts, you ask?
Management Concepts are the principles and practices managers use to manage people and resources. They cover topics like job descriptions (job descriptions), performance evaluations, training programmes, employee motivation and compensation systems.
How do you define Six Sigma?
Six-sigma will be well-known to anyone who has worked in operations research or statistics. It can be used by anyone in any business aspect.
This requires a lot of dedication, so only people with great leadership skills can make the effort to implement it.
What are the five management methods?
The five stages of any business are planning, execution, monitoring, review, and evaluation.
Planning is about setting goals for your future. Planning includes setting goals for the future.
Execution is when you actually execute the plans. It is important to ensure that everyone follows the plans.
Monitoring is checking on progress towards achieving your objectives. Regular reviews of performance against budgets and targets should be part of this process.
At the end of every year, reviews take place. They are a chance to see if everything went smoothly during the year. If not, then it may be possible to make adjustments in order to improve performance next time.
After each year's review, evaluation occurs. It helps identify which aspects worked well and which didn't. It provides feedback about how people perform.
It can sometimes seem difficult to make business decisions.
Complex systems are often complex and have many moving parts. It is difficult for people in charge of businesses to manage multiple priorities simultaneously and also deal with uncertainty.
It is important to understand the effects of these factors on the system in order to make informed decisions.
This requires you to think about the purpose and function of each component. You then need to consider how those individual pieces interact with each other.
Ask yourself if there are hidden assumptions that have influenced your behavior. If you don't have any, it may be time to revisit them.
If you're still stuck after all this, try asking someone else for help. They might see things differently than you and may have some insights that could help find a solution.
What is the difference of leadership and management?
Leadership is all about influencing others. Management is about controlling others.
A leader inspires others while a manager directs them.
Leaders motivate people to succeed; managers keep workers on track.
A leader develops people; a manager manages people.
Statistics
- Your choice in Step 5 may very likely be the same or similar to the alternative you placed at the top of your list at the end of Step 4. (umassd.edu)
- This field is expected to grow about 7% by 2028, a bit faster than the national average for job growth. (wgu.edu)
- Hire the top business lawyers and save up to 60% on legal fees (upcounsel.com)
- Our program is 100% engineered for your success. (online.uc.edu)
- 100% of the courses are offered online, and no campus visits are required — a big time-saver for you. (online.uc.edu)
External Links
How To
How can Lean Manufacturing be done?
Lean Manufacturing is a method to reduce waste and increase efficiency using structured methods. These processes were created by Toyota Motor Corporation, Japan in the 1980s. The aim was to produce better quality products at lower costs. Lean manufacturing seeks to eliminate unnecessary steps and activities in the production process. It is composed of five fundamental elements: continuous improvement; pull systems, continuous improvements, just-in–time, kaizen, continuous change, and 5S. Pull systems are able to produce exactly what the customer requires without extra work. Continuous improvement is constantly improving upon existing processes. Just-in-time is when components and other materials are delivered at their destination in a timely manner. Kaizen means continuous improvement. Kaizen involves making small changes and improving continuously. The 5S acronym stands for sort in order, shine standardize and maintain. To achieve the best results, these five elements must be used together.
Lean Production System
Six key concepts make up the lean manufacturing system.
-
Flow - focus on moving material and information as close to customers as possible;
-
Value stream mapping - break down each stage of a process into discrete tasks and create a flowchart of the entire process;
-
Five S's: Sort, Shine Standardize, Sustain, Set In Order, Shine and Shine
-
Kanban is a visual system that uses visual cues like stickers, colored tape or stickers to keep track and monitor inventory.
-
Theory of Constraints - Identify bottlenecks in the process, and eliminate them using lean tools such kanban boards.
-
Just-in time - Get components and materials delivered right at the point of usage;
-
Continuous improvement - incremental improvements are made to the process, not a complete overhaul.