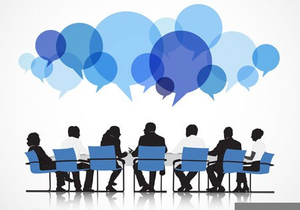
Resisting change can be a common psychological reaction to change. It can stem from fear, uncertainty, or fear. There are many solutions to these problems. These strategies reduce resistance to change and can help create an environment that is open to change.
Fear of the Unknown
Fear of unknown is a powerful emotion. Courage is required to overcome it. This emotion occurs when we don’t have enough data to make a decision. It can also manifest itself in an intolerance of uncertainty. There are many strategies to manage this fear, such as making a plan and practicing mindfulness. You can also talk to a trusted friend. A healthy lifestyle can help you overcome fear of the unknown.
Fear of the unknown is often accompanied by self-doubt. This can cause you to doubt your abilities and feel lost of control. It also inhibits your personal growth and hinders organisational progress. Procrastination can also be a result.
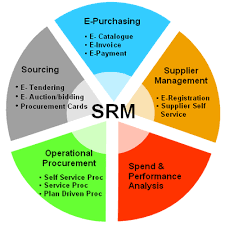
Incertitude
Uncertainty and fear are two of the top reasons people resist change. People tend to avoid the unknown because they fear the unknown. This inertia can easily be overcome by making sure that the process of changing is clear. Leaders should give as much information as they can and acknowledge the effects of any pending change.
Insecurity
Understanding the root causes and reasons behind insecurity that prevents you from changing is the first step to overcome it. Insecurity is a problem that affects all people in one way or another. Many people resist change for various reasons. These could be logical security concerns or economic concerns.
Insecurity is a natural reaction that changes can cause and it has many causes. Insecurity can lead to violent reactions for many people. People can lose their jobs or their status, which can be extremely frightening. Even small changes can have a profound impact on individuals.
Control of the situation is difficult
Fear of change can be a major reason why companies resist making organizational changes. Fear of change is often caused by mistrust or misunderstanding. People can feel threatened by being assigned a new manager to their team and may push back. Listening to employees can often be the best way of minimizing the effects.
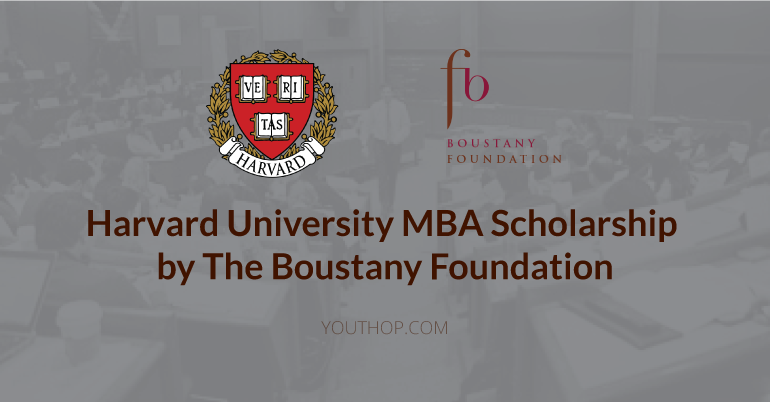
Lack of communication: People resist change due to ineffective communication. Leaders need to communicate clearly to employees the objectives and measures of change. Inability to communicate clearly and easily can hinder efforts to implement change.
FAQ
What is the difference between Six Sigma Six Sigma and TQM?
The main difference in these two quality management tools lies in the fact that six sigma is focused on eliminating defects and total quality management (TQM), emphasizes improving processes and reducing costs.
Six Sigma is a method for continuous improvement. This approach emphasizes eliminating defects through statistical methods like control charts, Pareto analysis, and p-charts.
This method has the goal to reduce variation of product output. This is accomplished by identifying the root cause of problems and fixing them.
Total quality management involves measuring and monitoring all aspects of the organization. This includes training employees to improve their performance.
It is frequently used as an approach to increasing productivity.
What is Kaizen?
Kaizen, a Japanese term that means "continuous improvement," is a philosophy that encourages employees and other workers to continuously improve their work environment.
Kaizen is based on the belief that every person should be able to do his or her job well.
What role can a manager fill in a company’s management?
There are many roles that a manager can play in different industries.
Managers generally oversee the day-today operations of a business.
He/she ensures the company meets its financial commitments and produces goods/services that customers demand.
He/she is responsible for ensuring that employees comply with all regulations and follow quality standards.
He/she plans and oversees marketing campaigns.
What is TQM, exactly?
The quality movement was born during the industrial revolution when manufacturing companies realized they could not compete on price alone. They needed to improve quality and efficiency if they were going to remain competitive.
Management developed Total Quality Management to address the need for improvement. It focused on all aspects of an organisation's performance. It included continual improvement processes, employee involvement, customer satisfaction, and customer satisfaction.
Statistics
- As of 2020, personal bankers or tellers make an average of $32,620 per year, according to the BLS. (wgu.edu)
- Your choice in Step 5 may very likely be the same or similar to the alternative you placed at the top of your list at the end of Step 4. (umassd.edu)
- The average salary for financial advisors in 2021 is around $60,000 per year, with the top 10% of the profession making more than $111,000 per year. (wgu.edu)
- Our program is 100% engineered for your success. (online.uc.edu)
- UpCounsel accepts only the top 5 percent of lawyers on its site. (upcounsel.com)
External Links
How To
How can you implement the Kaizen technique?
Kaizen means continuous improvement. This Japanese term refers to the Japanese philosophy of continuous improvement that emphasizes incremental improvements and constant improvement. It is a process where people come together to improve their processes.
Kaizen is one method that Lean Manufacturing uses to its greatest advantage. Employees responsible for the production line should identify potential problems in the manufacturing process and work together to resolve them. This increases the quality of products and reduces the cost.
The main idea behind kaizen is to make every worker aware of what happens around him/her. To prevent problems from happening, any problem should be addressed immediately. If someone spots a problem while at work, they should immediately report it to their manager.
Kaizen is based on a few principles. When working with kaizen, we always start with the end result and move towards the beginning. We can improve the factory by first fixing the machines that make it. Next, we repair the machines that make components. Then, the machines that make raw materials. Then, we fix those who work directly with the machines.
This approach is called 'kaizen' because it focuses on improving everything steps by step. We finish fixing the factory and then go back to the beginning. This continues until we achieve perfection.
You need to know how to measure the effectiveness of kaizen within your business. There are many methods to assess if kaizen works well. One way is to examine the amount of defects on the final products. Another way to find out how productive your company has been since you implemented kaizen is to measure the increase in productivity.
A good way to determine whether kaizen has been implemented is to ask why. You were trying to save money or obey the law? Did you really think that it would help you achieve success?
Congratulations if you answered "yes" to any of the questions. You are now ready to begin kaizen.