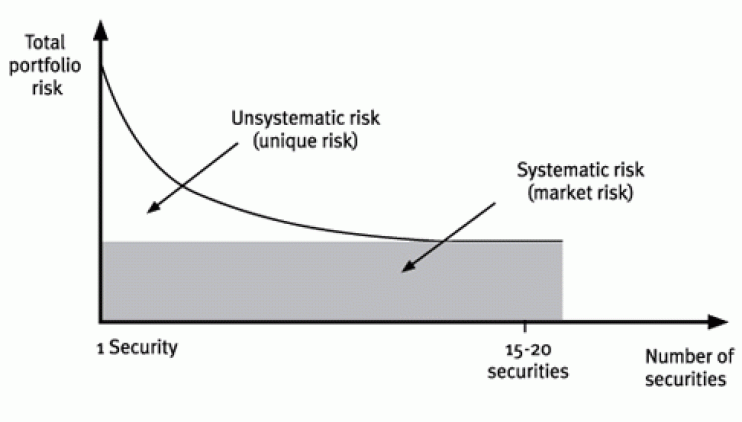
It's easy to get lost in the sea of resources and tools that project management offers. You're not the only one. Many project managers over the years have tried different techniques and tools, and developed their own strategies for making the most of their resources. It is important to make the most out of these tools and to learn more about each type of project management.
Common project management software
There are many tools for project management today. Gantt charts are one of the most commonly used tools for project management. This allows the team to track the progress of a project and shows the interdependencies among its various stages. The Gantt chart is great for software development, product construction and other areas where the team must deal with many deliverables.
Common project management certifications
Project managers who are industry-recognized certified have an advantage over counterparts. They will not only gain more knowledge but they will also be recognized and trusted in the industry. PMP stands for Project Management Professional and PRINCE2, for Projects IN Controlled Environments. These are two common certifications. These certifications can be acquired by new entrants to project management or by people with several years of experience in the field.
Common project management books
There are two main types of project management books. One is the PMBOK, which contains the entire A-Z vocabulary of project management terms. This type of book is best for certification candidates. However, it's not practical for anyone else. The project management handbook is another option, and it can be applied to any type of project, industry or niche.
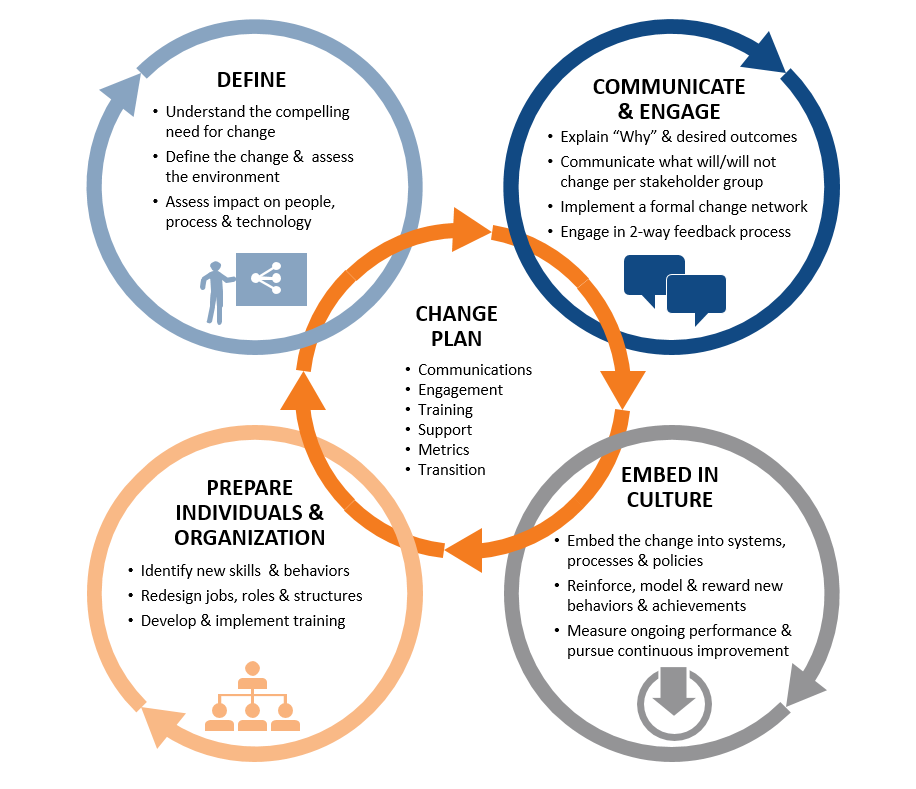
Common project management podcasts
Podcasts about project managing are a great resource for improving your knowledge. These podcasts are great for anyone, no matter how experienced or new you may be in project management. Moreover, these podcasts are widely available and you can listen to them from anywhere.
FAQ
What is Six Sigma?
This is a method of quality improvement that emphasizes customer service, continuous learning, and customer service. The goal is to eliminate defects by using statistical techniques.
Six Sigma was developed at Motorola in 1986 as part of its efforts to improve manufacturing processes.
The idea spread quickly throughout the industry, and today, many organizations are using six sigma methods to improve product design, production, delivery, and customer service.
Six Sigma is so popular.
Six Sigma can be implemented quickly and produce impressive results. Six Sigma provides a framework to measure improvements and allows companies to focus on the most important things.
What are the steps involved in making a decision in management?
The decision-making process for managers is complex and multifaceted. It involves many factors, such as analysis and strategy, planning, execution, measurement, evaluation, feedback etc.
Management of people requires that you remember that they are just as human as you are, and can make mistakes. You can always improve your performance, provided you are willing to make the effort.
This video shows you how management makes decisions. We discuss different types of decisions as well as why they are important and how managers can navigate them. The following topics will be covered:
What are the five management processes?
Each business has five stages: planning, execution and monitoring.
Setting goals for the future requires planning. It includes defining what you want to achieve and how you plan to do it.
Execution is the actual execution of the plans. You need to make sure they're followed by everyone involved.
Monitoring is checking on progress towards achieving your objectives. Monitoring should include regular reviews of performance against goals and budgets.
Review events take place at each year's end. They are a chance to see if everything went smoothly during the year. If not then, you can make changes to improve your performance next year.
After the annual review, evaluation takes place. It helps you identify the successes and failures. It also provides feedback on how well people performed.
What's the difference between leadership & management?
Leadership is about influencing others. Management is about controlling others.
A leader inspires others while a manager directs them.
A leader motivates people to achieve success; a manager keeps workers on task.
A leader develops people; a manager manages people.
Statistics
- Your choice in Step 5 may very likely be the same or similar to the alternative you placed at the top of your list at the end of Step 4. (umassd.edu)
- As of 2020, personal bankers or tellers make an average of $32,620 per year, according to the BLS. (wgu.edu)
- The BLS says that financial services jobs like banking are expected to grow 4% by 2030, about as fast as the national average. (wgu.edu)
- This field is expected to grow about 7% by 2028, a bit faster than the national average for job growth. (wgu.edu)
- Our program is 100% engineered for your success. (online.uc.edu)
External Links
How To
How does Lean Manufacturing work?
Lean Manufacturing is a method to reduce waste and increase efficiency using structured methods. They were created in Japan by Toyota Motor Corporation during the 1980s. It was designed to produce high-quality products at lower prices while maintaining their quality. Lean manufacturing eliminates unnecessary steps and activities from a production process. It consists of five basic elements: pull systems, continuous improvement, just-in-time, kaizen (continuous change), and 5S. The production of only what the customer needs without extra work is called pull systems. Continuous improvement is constantly improving upon existing processes. Just-in time refers to components and materials being delivered right at the place they are needed. Kaizen is continuous improvement. This can be achieved by making small, incremental changes every day. Finally, 5S stands for sort, set in order, shine, standardize, and sustain. These five elements are combined to give you the best possible results.
Lean Production System
The lean production system is based on six key concepts:
-
Flow - focuses on moving information and materials as close to customers as possible.
-
Value stream mapping: This is a way to break down each stage into separate tasks and create a flowchart for the entire process.
-
Five S's: Sort, Shine Standardize, Sustain, Set In Order, Shine and Shine
-
Kanban - visual cues such as stickers or colored tape can be used to track inventory.
-
Theory of constraints: Identify bottlenecks and use lean tools such as kanban boards to eliminate them.
-
Just-in Time - Send components and material directly to the point-of-use;
-
Continuous improvement - make incremental improvements to the process rather than overhauling it all at once.