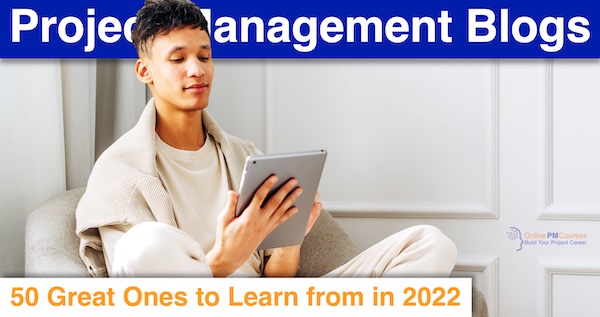
A team can find it difficult to follow a self-managed plan, but it can also make things easier. You will learn about the benefits and drawbacks of self-managed groups and how to implement them within your team. You will be able, after reading this article to decide if self-managed teams is right for you. For a deeper discussion, continue reading.
Disadvantages of self-managed teams
There are many benefits to self-managed groups in your business. The structure provides more flexibility but can also create power vacuums in your team. While some people will assume leadership roles, others will be more comfortable with their responsibilities. Additionally, self-managed groups are not accountable for their management. This makes it difficult for executives to influence the team, which can result in a lack of productivity and creativity.
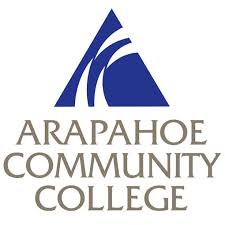
Self-managed organizations can have the disadvantage of being ineffective in enhancing organizational performance. Managers should clearly outline their responsibilities to their teams and delegate authority. This will make them more productive. Managers can also fail to achieve their goals if they manage the team themselves. A manager should be a part of self-managed groups. He or she should hold the team responsible for their results and give feedback to members.
The challenges of self-managed groups
There are many benefits to self-managed groups. These teams are usually more efficient than traditional team, and can communicate quickly and take steps to implement their ideas. These teams are more likely to be innovative as they assume responsibility for their own work. There are downsides, however. Although self-managed groups may be better for some companies, it is important to take into account their advantages before you make a decision. Below we will look at some of the benefits and challenges of self-managed teams.
The self-managed team can boost productivity and individual commitment. The problem with self-directed groups is that members may specialize in one area, which can limit collaboration and shared commitment. This can be solved by having a voting system so that team members can agree on a course and vote on the decision. Self-managed teams are less collaborative than traditional teams due to a lack of cross-team communication.
Here are some ways to make self-managed team members
In order to establish self-managed and accountable teams, one of the best ways is to foster a culture where everyone can be accountable. Instead of traditional teams where each member takes responsibility for their own decisions, self-managed groups are driven by the commitments made by all members. These commitments make the work move forward because members recognize both their individual and collective responsibilities. This sense of accountability is emphasized throughout the entire team. This atmosphere of accountability encourages creativity and innovation.
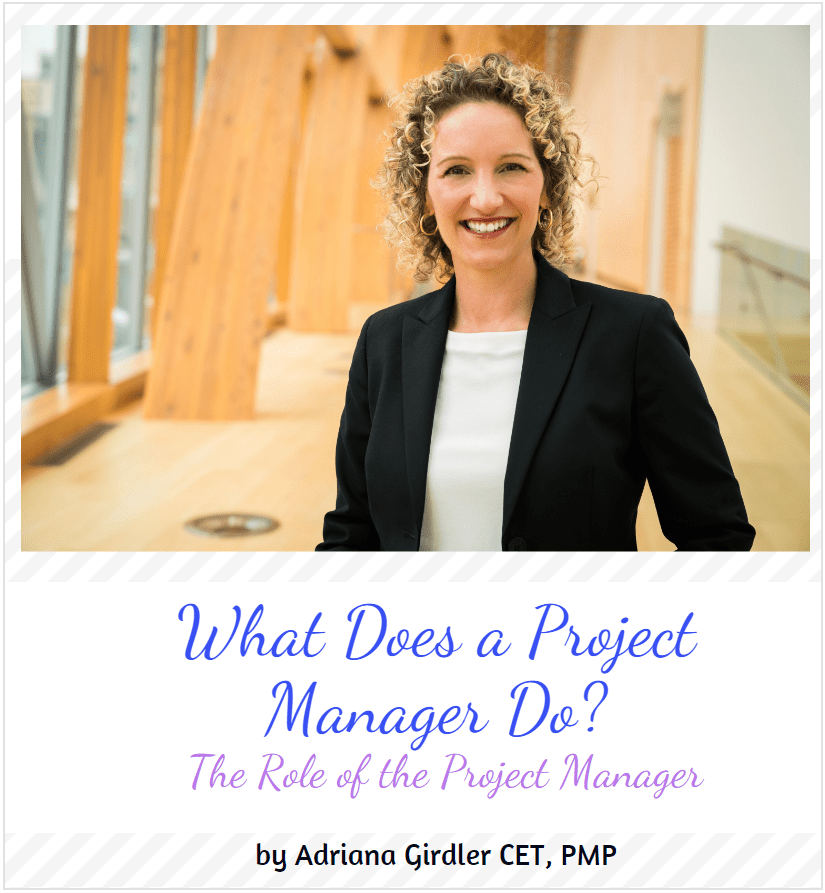
It is important to define clear goals, tasks and milestones in order to create a self managing team. You can set clear metrics for the team to measure its progress. For example, you might want to lead the industry in net promoter scores. You may need to hire additional members if the self-managed group is not yet established. To ensure that employees are able to understand the changes, it is a good idea to train them.
FAQ
What is the difference in leadership and management?
Leadership is about being a leader. Management is about controlling others.
A leader inspires followers while a manager directs workers.
A leader motivates people and keeps them on task.
A leader develops people; a manager manages people.
What are the five management steps?
The five stages of a business include planning, execution (monitoring), review, evaluation, and review.
Planning involves setting goals for the future. Planning includes setting goals for the future.
Execution takes place when you actually implement the plans. You need to make sure they're followed by everyone involved.
Monitoring is the act of monitoring your progress towards achieving your targets. Monitoring should include regular reviews of performance against goals and budgets.
Each year, reviews are held at the end. They provide an opportunity to assess whether everything went well during the year. If not, it is possible to make improvements for next year.
After each year's review, evaluation occurs. It helps identify what worked well and what didn't. It also provides feedback on how well people performed.
What are management concepts?
Management concepts are the principles and practices used by managers to manage people, resources. These topics include job descriptions, performance evaluations and training programs. They also cover human resource policies, job description, job descriptions, job descriptions, employee motivation, compensation systems, organizational structures, and many other topics.
Statistics
- 100% of the courses are offered online, and no campus visits are required — a big time-saver for you. (online.uc.edu)
- As of 2020, personal bankers or tellers make an average of $32,620 per year, according to the BLS. (wgu.edu)
- Your choice in Step 5 may very likely be the same or similar to the alternative you placed at the top of your list at the end of Step 4. (umassd.edu)
- Hire the top business lawyers and save up to 60% on legal fees (upcounsel.com)
- The profession is expected to grow 7% by 2028, a bit faster than the national average. (wgu.edu)
External Links
How To
What is Lean Manufacturing?
Lean Manufacturing processes are used to reduce waste and improve efficiency through structured methods. They were created in Japan by Toyota Motor Corporation during the 1980s. It was designed to produce high-quality products at lower prices while maintaining their quality. Lean manufacturing focuses on eliminating unnecessary steps and activities from the production process. It includes five main elements: pull systems (continuous improvement), continuous improvement (just-in-time), kaizen (5S), and continuous change (continuous changes). Pull systems involve producing only what the customer wants without any extra work. Continuous improvement involves constantly improving upon existing processes. Just-in-time refers to when components and materials are delivered directly to the point where they are needed. Kaizen means continuous improvement. Kaizen involves making small changes and improving continuously. The 5S acronym stands for sort in order, shine standardize and maintain. To achieve the best results, these five elements must be used together.
Lean Production System
Six key concepts form the foundation of the lean production system:
-
Flow - focus on moving material and information as close to customers as possible;
-
Value stream mapping- This allows you to break down each step of a process and create a flowchart detailing the entire process.
-
Five S's: Sort, Shine Standardize, Sustain, Set In Order, Shine and Shine
-
Kanban - visual cues such as stickers or colored tape can be used to track inventory.
-
Theory of Constraints - Identify bottlenecks in the process, and eliminate them using lean tools such kanban boards.
-
Just-in-time delivery - Deliver components and materials right to your point of use.
-
Continuous improvement - incremental improvements are made to the process, not a complete overhaul.