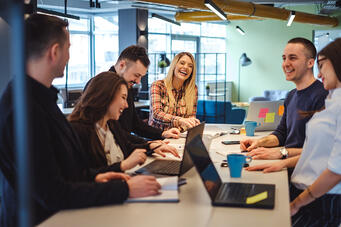
If you haven't heard of management of change (MOC), then you should. This best practice can help you avoid unwanted consequences and keep your company running smoothly. More information about MOC (and its stages) can be found below. Here are eight essential MOC stages. You'll be able successfully manage changes in your company if you follow these steps. So, what exactly is MOC and how can you use it to manage change in your organization? What is MOC? Why does it matter?
MOC refers to a process
MOC is often overlooked within organizations. Because of inexperience and a lack process safety information, workplace accidents can be caused by changes. Companies rush through changes to get them done, but neglect to manage risk. Changes to existing production procedures and systems can lead to accidents if the organization is not in the process for redesigning them. This is especially true in the case of industries that deal with dangerous substances and energy.
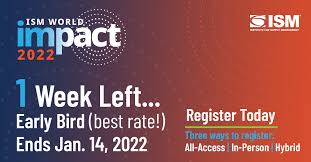
It consists in eight stages
McKinsey's Model for Change Management describes change as an architectural process. There are eight stages to the McKinsey model: preparation, implementation monitoring, evaluation and sustainability. The first three stages are focused on the business aspect of change. The second two focus on the emotional aspects. Culture must be considered in the eighth stage. New practices need to be embraced within existing work cultures. To ensure that successful change management is possible, the organization's culture should be able adapt to the changes.
It prevents unintended consequences
Unintended consequences are caused by people who don't always reflect on their actions before making a choice. For example, people may make decisions based on past performance rather than analyzing the current situation. Unintended consequences could result and may ultimately prove to be counterproductive. There are many ways to manage change and minimize unwanted consequences. Implementing a new process can have unintended positive and negative consequences. For example, if a new technology is introduced, a test group will be established to assess its impact.
It is a good practice
Management of change is a key factor in ensuring a better future. This best practice can be used to help create an organizational shift. It's important not to forget that there are many other elements to change management. These elements are crucial to any change management project's success. These factors should be taken into consideration to ensure that the whole process of change is smooth.
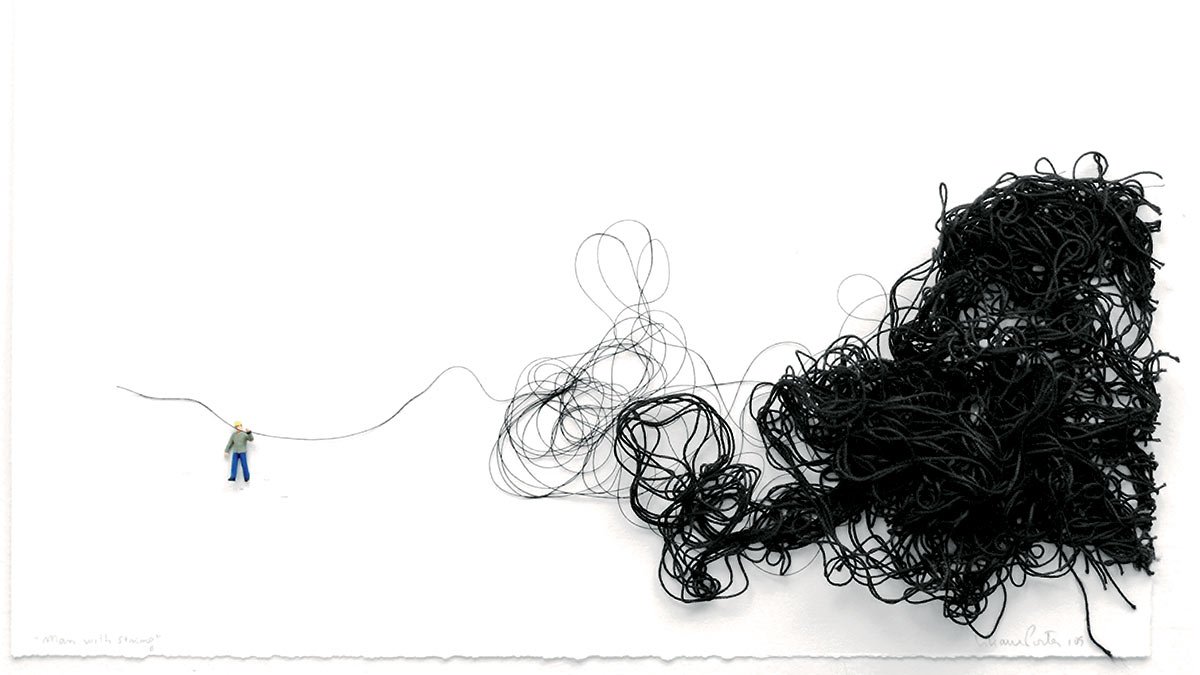
It is important to maintain regulatory compliance
Organizations must report on and monitor processes to maintain compliance with regulatory requirements. These metrics can be used to assess process adherence and determine risks/performance indicators. In addition, metrics can help identify regulatory changes and the impact they will have on an organization. Organizations that monitor change can be proactive in anticipating future regulations and demonstrating compliance. This article will focus on the important metrics that should be monitored and reported.
FAQ
What kind of people use Six Sigma?
Six Sigma is well-known to those who have worked in operations research and statistics. Anybody involved in any aspect or business can benefit.
This requires a lot of dedication, so only people with great leadership skills can make the effort to implement it.
Why does it sometimes seem so hard to make good business decisions
Complex systems are often complex and have many moving parts. People who manage them have to balance multiple priorities while dealing with complexity and uncertainty.
It is important to understand the effects of these factors on the system in order to make informed decisions.
It is important to consider the functions and reasons for each part of the system. You then need to consider how those individual pieces interact with each other.
It is also worth asking yourself if you have any unspoken assumptions about how you have been doing things. If you don't have any, it may be time to revisit them.
For help, ask someone else if you're still stumped after all the above. You might find their perspective is different from yours and they may have insight that can help you find the solution.
What is the best way to motivate your employees as a manager?
Motivation is the desire for success.
Engaging in something fun can be a great way to get motivated.
You can also be motivated by the idea of making a difference to the success and growth of your organization.
For example, if your goal is to become a physician, you will probably find it more motivational to see patients rather than to read a lot of medicine books.
The inner motivation is another type.
One example is a strong sense that you are responsible for helping others.
You may even find it enjoyable to work hard.
Ask yourself why you feel so motivated.
Then try to think about ways to change your situation to be more motivated.
Six Sigma is so popular.
Six Sigma can be implemented quickly and produce impressive results. Six Sigma provides a framework to measure improvements and allows companies to focus on the most important things.
What is the difference between a project and a program?
A project is temporary while a programme is permanent.
A project has usually a specified goal and a time limit.
It is often carried out by a team of people who report back to someone else.
A program is usually defined by a set or goals.
It is often implemented by one person.
What is the difference of leadership and management?
Leadership is about influence. Management is about controlling others.
A leader inspires followers while a manager directs workers.
Leaders inspire people to achieve success. Managers keep their workers focused.
A leader develops people; a manager manages people.
Statistics
- As of 2020, personal bankers or tellers make an average of $32,620 per year, according to the BLS. (wgu.edu)
- The average salary for financial advisors in 2021 is around $60,000 per year, with the top 10% of the profession making more than $111,000 per year. (wgu.edu)
- UpCounsel accepts only the top 5 percent of lawyers on its site. (upcounsel.com)
- Hire the top business lawyers and save up to 60% on legal fees (upcounsel.com)
- Our program is 100% engineered for your success. (online.uc.edu)
External Links
How To
What is Lean Manufacturing?
Lean Manufacturing techniques are used to reduce waste while increasing efficiency by using structured methods. They were developed in Japan by Toyota Motor Corporation (in the 1980s). The goal was to produce quality products at lower cost. Lean manufacturing focuses on eliminating unnecessary steps and activities from the production process. It consists of five basic elements: pull systems, continuous improvement, just-in-time, kaizen (continuous change), and 5S. Pull systems involve producing only what the customer wants without any extra work. Continuous improvement means continuously improving on existing processes. Just-in–time refers when components or materials are delivered immediately to their intended destination. Kaizen means continuous improvement, which is achieved by implementing small changes continuously. Last but not least, 5S is for sort. These five elements work together to produce the best results.
Lean Production System
The lean production system is based on six key concepts:
-
Flow - focus on moving material and information as close to customers as possible;
-
Value stream mapping - Break down each stage in a process into distinct tasks and create an overview of the whole process.
-
Five S's, Sort, Set in Order, Shine. Standardize. and Sustain.
-
Kanban – visual signals like colored tape, stickers or other visual cues are used to keep track inventory.
-
Theory of Constraints - Identify bottlenecks in the process, and eliminate them using lean tools such kanban boards.
-
Just-intime - Order components and materials at your location right on the spot.
-
Continuous improvement - make incremental improvements to the process rather than overhauling it all at once.