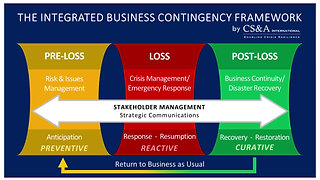
If you are looking for a project management blog, there are several excellent options. This article will cover John's Project Managementblog, Capterra’s Project Management blog, and NTask’s Project Management blog. Each blog will offer useful information on a wide range of topics in project management. The blog offers valuable information and advice.
John's blog on project management
John's blog on project management is a must-read for project managers. His posts have an informal tone that appeals to all levels of project manager. His blog is a great resource for all levels of project management, new and experienced alike. Information on agile, project managing, and team building will be found in his blog. John's blog has everything you need to know about project management.
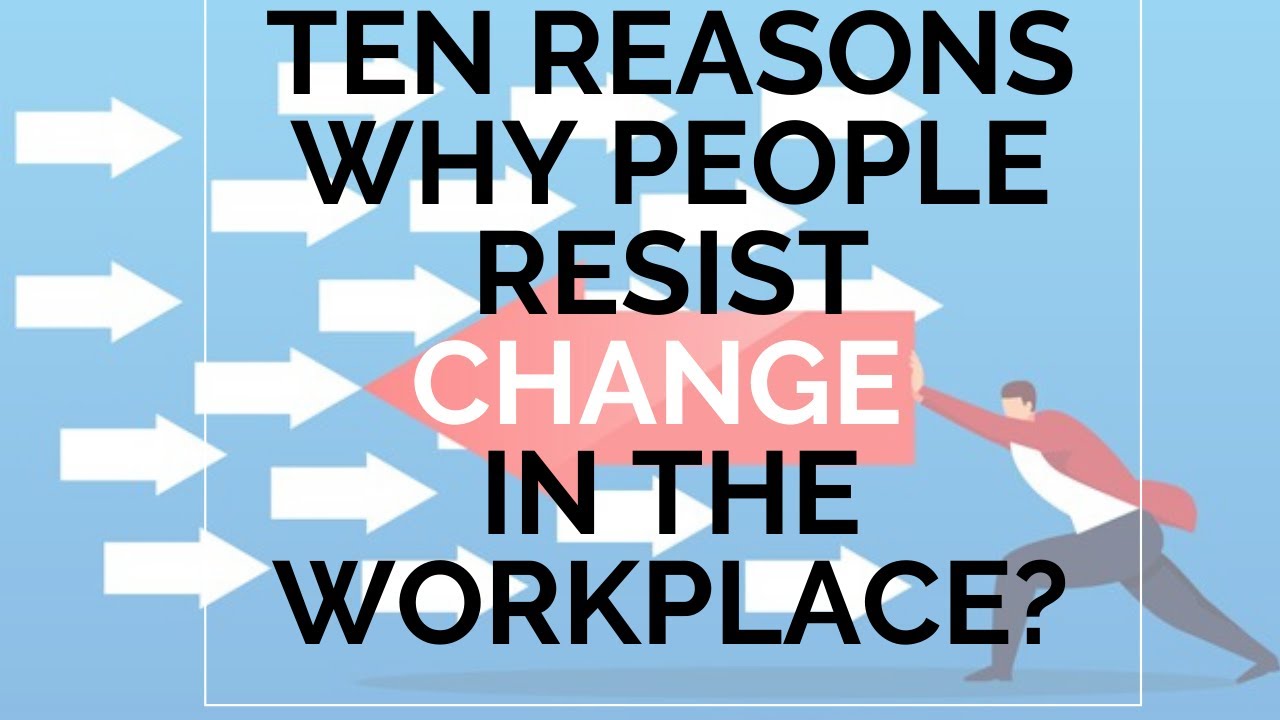
John Goodpasture, an expert in project management, wrote this blog. You'll find interesting posts and thought-provoking queries on this site. The IIL's blog on project management is a great resource for project managers looking for more information. It's a one-stop shop for educational materials, templates, and white papers. The IIL, a world-class business education institution, has a project management blog that is an excellent resource for project management information.
Capterra's blog on project management
When it comes to choosing project management software, Capterra is the go-to source. The blog provides real reviews and insights. It also offers helpful guides and comparisons. By providing these resources, Capterra's project management blog can be an invaluable resource for project managers in every stage of the process. It also discusses productivity, an important topic for every business.
Rachel has recently left Capterra and wrote the Capterra project blog. She also wrote numerous articles while working at Capterra. She has since left Capterra, but she still uses Twitter for her personal thoughts. In addition to blogging about project management, Rachel also writes about the latest trends in the industry and offers her thoughts on Twitter. Her experience spans more than twenty years and she is the author of several books and articles.
The project management blog of NTask
Blogs on project management are an excellent resource. The NTask blog on project management is a great resource for information about various types of projects. It covers a variety topics and is kept current. It contains all the information project managers need to be successful. In addition to providing helpful information, NTask's blog also features useful resources to help project managers improve their performance. The NTask blog features articles from experienced project managers.
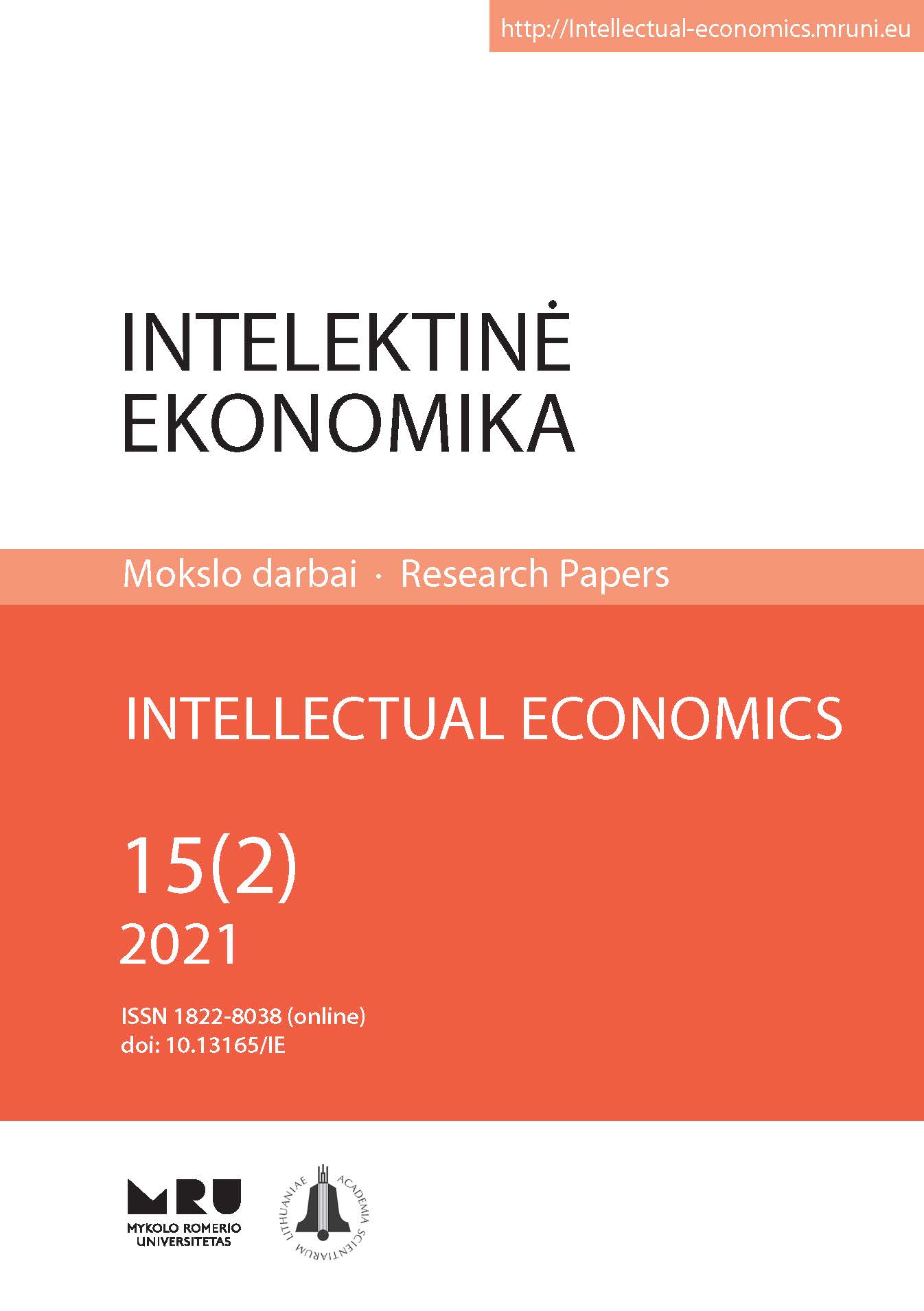
NTask's project management website offers useful tips and articles on collaboration, productivity, resource management, and multi-project management. The site's layout is easy to navigate, and the articles are incredibly clear and informative. A blog like this is great for beginners. It has a simple, clear style that will appeal to everyone. NTask offers a wealth of information for project managers from all levels.
FAQ
Six Sigma is so popular.
Six Sigma can be implemented quickly and produce impressive results. Six Sigma also gives companies a framework for measuring improvement and helps them focus on what is most important.
What is Kaizen?
Kaizen, a Japanese term that means "continuous improvement," is a philosophy that encourages employees and other workers to continuously improve their work environment.
Kaizen is based on the belief that every person should be able to do his or her job well.
How do you manage your employees effectively?
The key to effective management of employees is ensuring their happiness and productivity.
This includes setting clear expectations for their behavior and tracking their performance.
Managers must be clear about their goals and those of their teams in order to succeed.
They need to communicate clearly with staff members. They also need to make sure that they discipline and reward the best performers.
They also need to keep records of their team's activities. These include:
-
What did you accomplish?
-
How much work was done?
-
Who did it?
-
How did it get done?
-
Why was this done?
This information can be used to monitor performance and evaluate results.
What are the 3 basic management styles?
These are the three most common management styles: participative (authoritarian), laissez-faire (leavez-faire), and authoritarian. Each style is unique and has its strengths as well as weaknesses. Which style do YOU prefer? Why?
Authoritarian - The leader sets the direction and expects everyone to comply with it. This style works best if the organization is large and stable.
Laissez-faire – The leader gives each individual the freedom to make decisions for themselves. This style is most effective when the organization's size and dynamics are small.
Participative - The leader listens to ideas and suggestions from everyone. This style works best in smaller organizations where everyone feels valued.
What is the difference between Six Sigma Six Sigma and TQM?
The main difference in these two quality management tools lies in the fact that six sigma is focused on eliminating defects and total quality management (TQM), emphasizes improving processes and reducing costs.
Six Sigma can be described as a strategy for continuous improvement. It emphasizes the elimination of defects by using statistical methods such as control charts, p-charts, and Pareto analysis.
The goal of this method is to reduce variation in product output. This is done by identifying root causes and rectifying them.
Total quality management involves measuring and monitoring all aspects of the organization. Training employees is also part of total quality management.
It is frequently used as an approach to increasing productivity.
What is TQM exactly?
When manufacturing companies realized that price was not enough to compete, the industrial revolution brought about the quality movement. To remain competitive, they had to improve quality as well as efficiency.
Management responded to the need to improve, and developed Total Quality Management (TQM). This focused on improving every aspect of an organization’s performance. It included continuous improvement and employee involvement as well as customer satisfaction.
How does Six Sigma function?
Six Sigma uses statistics to measure problems, find root causes, fix them, and learn from past mistakes.
The first step to solving the problem is to identify it.
Next, data will be collected and analyzed to determine trends and patterns.
Then corrective actions are taken to solve the problem.
Finally, data will be reanalyzed to determine if there is an issue.
This continues until the problem has been solved.
Statistics
- Our program is 100% engineered for your success. (online.uc.edu)
- The average salary for financial advisors in 2021 is around $60,000 per year, with the top 10% of the profession making more than $111,000 per year. (wgu.edu)
- This field is expected to grow about 7% by 2028, a bit faster than the national average for job growth. (wgu.edu)
- UpCounsel accepts only the top 5 percent of lawyers on its site. (upcounsel.com)
- The profession is expected to grow 7% by 2028, a bit faster than the national average. (wgu.edu)
External Links
How To
How is Lean Manufacturing done?
Lean Manufacturing is a method to reduce waste and increase efficiency using structured methods. They were developed by Toyota Motor Corporation in Japan during the 1980s. The goal was to produce quality products at lower cost. Lean manufacturing eliminates unnecessary steps and activities from a production process. It is made up of five elements: continuous improvement, continuous improvement, just in-time, continuous change, and 5S. The production of only what the customer needs without extra work is called pull systems. Continuous improvement is the continuous improvement of existing processes. Just-in–time refers when components or materials are delivered immediately to their intended destination. Kaizen means continuous improvement, which is achieved by implementing small changes continuously. Finally, 5S stands for sort, set in order, shine, standardize, and sustain. These five elements work together to produce the best results.
The Lean Production System
Six key concepts underlie the lean production system.
-
Flow: The goal is to move material and information as close as possible from customers.
-
Value stream mapping: This is a way to break down each stage into separate tasks and create a flowchart for the entire process.
-
Five S's, Sort, Set in Order, Shine. Standardize. and Sustain.
-
Kanban – visual signals like colored tape, stickers or other visual cues are used to keep track inventory.
-
Theory of Constraints - Identify bottlenecks in the process, and eliminate them using lean tools such kanban boards.
-
Just-in-time delivery - Deliver components and materials right to your point of use.
-
Continuous improvement is making incremental improvements to your process, rather than trying to overhaul it all at once.