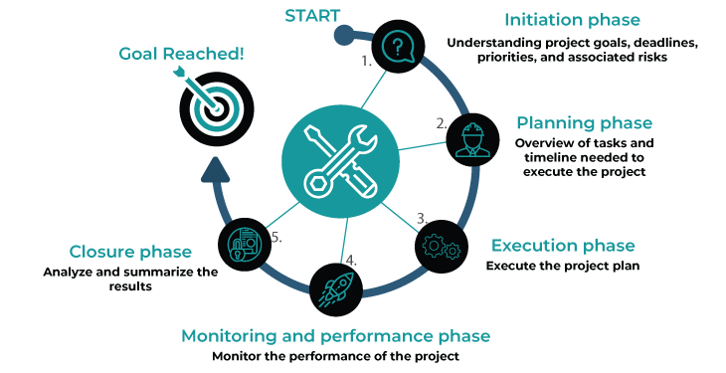
Your employees' well-being is dependent on a positive workplace environment. This will increase productivity, reduce burnout, and decrease complaints. Research has shown that employees who feel happy and motivated perform better. However, there are a number of things you should keep in mind before creating a positive working environment.
Positive working environment promotes productivity
A positive work environment creates a calm atmosphere that allows people to focus on their work and be more productive. This environment promotes cognitive and physical well-being, and it is often marked by clear communication between employees as well as management. This type environment encourages employees to learn and grow by offering them opportunities to ask questions as well as constructive feedback.
Moreover, a positive work environment encourages employees to give 200% of their best efforts. They are not afraid to take responsibility for their actions, and are not quick to play revenge games when given difficult feedback. It fosters friendship, camaraderie, and healthy competition. It encourages employees take breaks and enjoy the work they do.
Employees feel happier
You can make your employees happier by creating a positive environment at work. Happy employees are more productive and more inclined to share their ideas with colleagues. They also feel less stressed and more satisfied, and are less likely to take sick days.
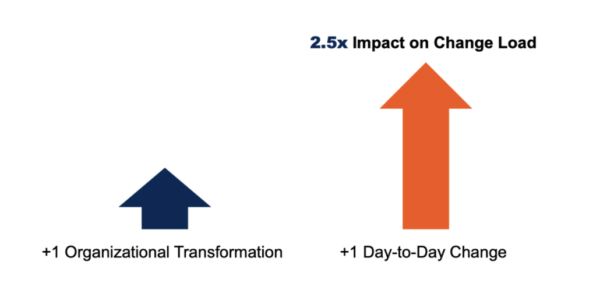
Research at the University of Birmingham has shown that creating a positive work environment can lead to greater employee happiness. When employees are happy, they work more efficiently, make more call-to-sale conversions per hour, and adhere to their workflow schedule.
You can reduce your burnout
Effective prevention strategies are vital to ensure that your organization is not at risk of losing its productivity and health. Burnout is a psychosocial condition that can impact working relationships. It's characterized by lack of empathy and emotional detachedness from patients or colleagues. Research has shown that proactive measures, such as creating a positive work environment, can prevent this condition.
Positive working environments have the ability to reduce burnout by boosting individual and team efficacy. Empowerment boosts individual efficacy. This helps to reduce the negative effects of cynicism and exhaustion. The quality of communication among staff increases team efficacy, which is related to personal efficacy.
It reduces complaints
A positive working environment helps employees feel good about their work. People who work in this environment are more likely be able to focus on their tasks and finish them on time. They are also more productive and have a higher employee status. Collaboration is also encouraged by a positive work environment. This allows employees to share their ideas and receive feedback that can help them improve their performance.
Positive working conditions for employees can reduce the amount of complaints made by employees. It is important to create a safe environment for employees that is free from bullying, harassment, and discrimination. It is great to work in a workplace free from harassment and discrimination. Positive working environments can improve employee morale as well as reduce complaints and employee stress.
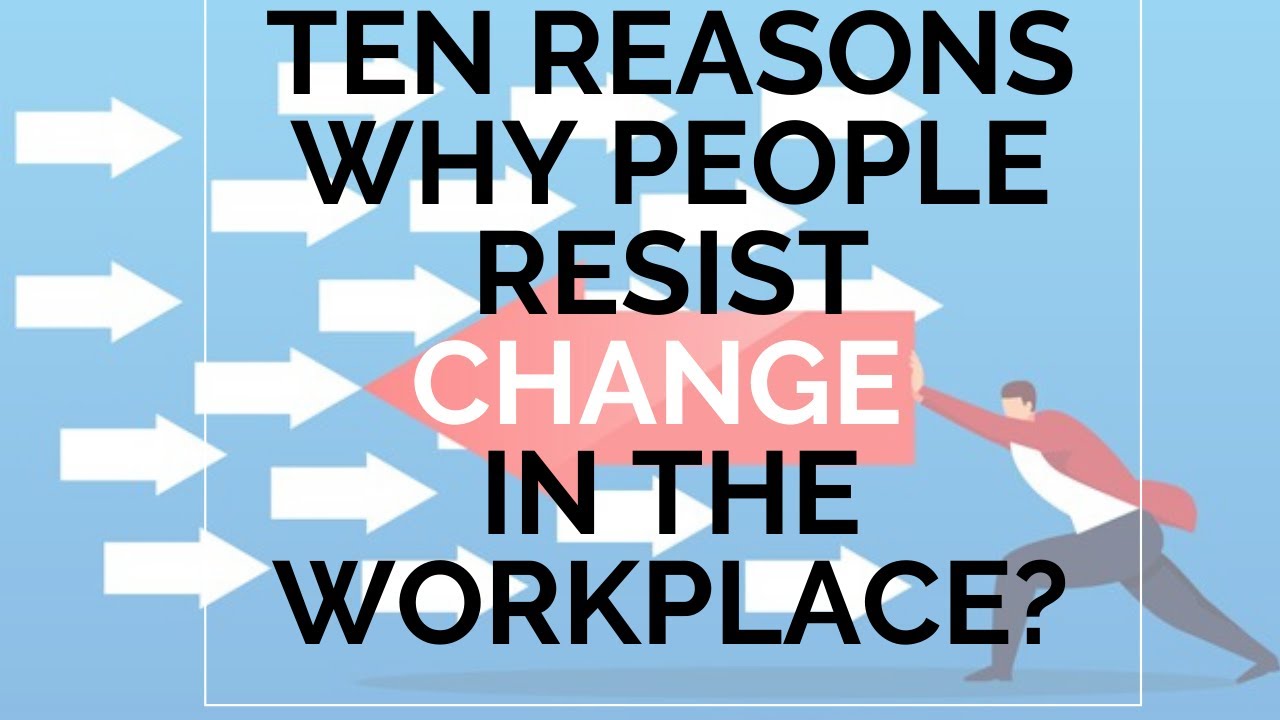
It improves teacher well-being
Teachers' wellbeing can be directly affected by how they work. There are many ways to improve teacher wellness, including providing a supportive environment for staff and hosting regular meetings. A school audit can help teachers assess their health and set goals to improve.
Teachers have to deal with a variety of interactions each day. The quality of these interactions is crucial to their well-being. Studies have shown that a toxic culture can lead to poor teacher wellbeing. Positive environments support healthy practice and help teachers focus on their students. Regular professional development is also important for educators. A survey found that teachers want PD for teacher well-being to be widely available and standard practice.
FAQ
How does Six Sigma work?
Six Sigma uses statistics to measure problems, find root causes, fix them, and learn from past mistakes.
The first step in solving a problem is to identify it.
Next, data will be collected and analyzed to determine trends and patterns.
Next, corrective steps are taken to fix the problem.
Final analysis of data is done to determine if the problem has been solved.
This continues until the problem has been solved.
What is the difference between leadership and management?
Leadership is about inspiring others. Management is about controlling others.
A leader inspires others while a manager directs them.
A leader motivates people and keeps them on task.
A leader develops people; a manager manages people.
What is Kaizen?
Kaizen, a Japanese term that means "continuous improvement," is a philosophy that encourages employees and other workers to continuously improve their work environment.
Kaizen is based upon the belief that each person should be capable of doing his or her job well.
What are management theories?
Management concepts are the principles and practices used by managers to manage people, resources. These topics include job descriptions, performance evaluations and training programs. They also cover human resource policies, job description, job descriptions, job descriptions, employee motivation, compensation systems, organizational structures, and many other topics.
What is Six Sigma?
This is a method of quality improvement that emphasizes customer service, continuous learning, and customer service. The goal is to eradicate defects through statistical techniques.
Motorola's 1986 efforts to improve manufacturing process efficiency led to the creation of Six Sigma.
The idea spread quickly in the industry. Today many organizations use six-sigma techniques to improve product design.
What are the key management skills?
Business owners need to have management skills, no matter how small or large they may be. These include the ability and willingness to manage people, finances as well resources, time and space.
These skills are necessary for setting goals and objectives as well as planning strategies, leading groups, motivating employees and solving problems.
As you can see, there's no end to the list of managerial duties!
Statistics
- 100% of the courses are offered online, and no campus visits are required — a big time-saver for you. (online.uc.edu)
- The profession is expected to grow 7% by 2028, a bit faster than the national average. (wgu.edu)
- UpCounsel accepts only the top 5 percent of lawyers on its site. (upcounsel.com)
- The average salary for financial advisors in 2021 is around $60,000 per year, with the top 10% of the profession making more than $111,000 per year. (wgu.edu)
- Hire the top business lawyers and save up to 60% on legal fees (upcounsel.com)
External Links
How To
How do I do the Kaizen Method?
Kaizen means continuous improvement. This term was first used by Toyota Motor Corporation in the 1950s. It refers to the Japanese philosophy that emphasizes continuous improvement through small incremental changes. This is a collaborative process in which people work together to improve their processes continually.
Kaizen is one of the most effective methods used in Lean Manufacturing. Employees responsible for the production line should identify potential problems in the manufacturing process and work together to resolve them. This way, the quality of products increases, and the cost decreases.
Kaizen is the idea that every worker should be aware of what is going on around them. If something is wrong, it should be corrected immediately so that no problem occurs. So, if someone notices a problem while working, he/she should report it to his/her manager.
Kaizen has a set of basic principles that we all follow. We always start from the end product and move toward the beginning. To improve our factory, for example, we need to fix the machines that produce the final product. Next, we fix the machines which produce components. We then fix the workers that work with those machines.
This method, called 'kaizen', focuses on improving each and every step of the process. Once we have finished fixing the factory, we return to the beginning and work until perfection.
You need to know how to measure the effectiveness of kaizen within your business. There are several ways to determine whether kaizen is working well. Another way to determine if kaizen is working well is to look at the quality of the products. Another way is to check how much productivity has grown since kaizen was implemented.
To determine if kaizen is effective, you should ask yourself why you chose to implement kaizen. You were trying to save money or obey the law? Did you really believe that it would be a success factor?
Congratulations if you answered "yes" to any of the questions. You are now ready to begin kaizen.