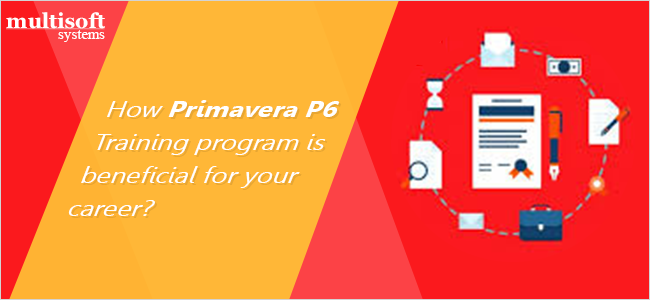
When creating a capacity planning strategy, you need to consider the expected growth of the workload, including any customer-driven growth and new features. Plan accordingly. Here are four common scenarios to consider: Lead, Lag, Match, Adjustment. Each scenario is unique and has its challenges as well as benefits. Each scenario has its own benefits and challenges. You need to carefully consider each one in order for your capacity planning to be effective.
Lead strategy
Companies that have a clear strategy for capacity planning will be more proactive in increasing capacity, expanding resources or expanding the system. A lag strategy on the other side waits until demand rises before expanding capacity. A lead strategy has the advantage that it doesn't run out of capacity in case of an unexpected rise in demand.
This strategy can be applied in many situations. It is most effective when there is a higher volume of goods or services than expected. It is also useful when demand is high, like during holidays. A retailer can increase its staffing levels by hiring seasonal workers during peak holiday seasons, for example. A lead strategy also allows for quick additions of headcount.
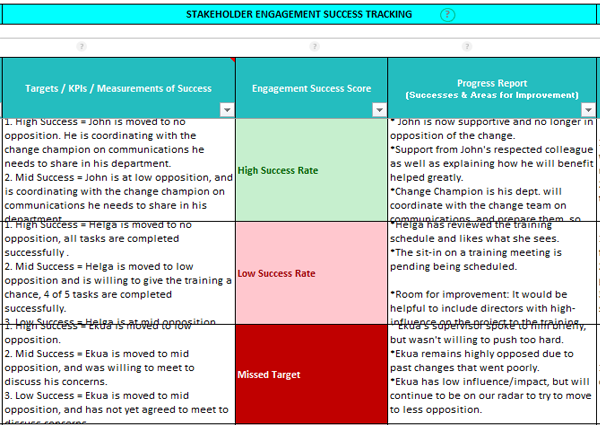
Lag strategy
The Lag strategy for capacity planning is used to match capacity to demand. This strategy is much less risky than Lead, but requires more work and effort. It also tends to be more risk-averse than the other two strategies. In contrast, the lead strategy tries to anticipate future demand and expand capacity accordingly. This strategy might not work for all organizations because of time constraints or resource limitations.
If a company has a stable business model, a lag plan is a good option. This strategy prevents excess inventory and waste by only increasing production when there is demand. This method can add stress to the process for hiring and training new workers. An aggressive lead strategy is, however, more aggressive. It anticipates future demands and meets them before their time.
Match strategy
The Match strategy can be described as the middle ground between Lead and Lag strategies in capacity planning. This strategy emphasizes incremental capacity increases, and not boosting demand ahead. It is more work to plan and implement, but it is safer for most manufacturers. While it may not be cheap to increase capacity, it is much safer than the two other strategies.
Match strategy includes monitoring current demand and forecast analysis. This allows the company's ability to quickly adapt to changes. Although it requires more effort, this strategy allows for fast and efficient pivots. It also helps streamline operations by ensuring that the resources available are adequate for the current and future demands.
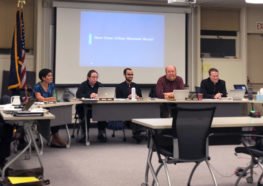
Adjustment strategy
An Adjustment strategy is a common way to manage supply chain capacity. It ensures that the supply chain is always ready to meet demand. It assists businesses in meeting their deadlines and scaling up their businesses. The key to maximizing your bottom line is choosing the right strategy. The Adjustment strategy can help organizations meet their supply-chain needs more efficiently.
It forces organizations to be more realistic about their resources. Overestimating the resources can result in lower productivity and lower worker morale. Over-allocating budgets can cause significant opportunity losses, since they could have gone towards continuous service improvement, innovation, pay, or employee compensation. This strategy also forces leaders to be more realistic in forecasting their budgets.
FAQ
What is Kaizen?
Kaizen is a Japanese term meaning "continuous improvement." It is a philosophy that encourages employees to constantly look for ways to improve their work environment.
Kaizen is built on the belief that everyone should be able do their jobs well.
How does Six Sigma work?
Six Sigma uses statistical analyses to locate problems, measure them, analyze root cause, fix problems and learn from the experience.
First, identify the problem.
Next, data will be collected and analyzed to determine trends and patterns.
The problem can then be fixed by taking corrective measures.
Finally, data is reanalyzed to determine whether the problem has been eliminated.
This cycle continues until there is a solution.
What is the difference between management and leadership?
Leadership is about influencing others. Management is about controlling others.
A leader inspires his followers while a manager directs the workers.
Leaders inspire people to achieve success. Managers keep their workers focused.
A leader develops people; a manager manages people.
Why is project management important for companies?
To ensure projects run smoothly and meet deadlines, project management techniques are employed.
This is because most businesses rely on project work for their products and services.
Companies need to manage these projects efficiently and effectively.
Companies can lose time, money, and reputation if they don't have a good project management system.
Statistics
- The average salary for financial advisors in 2021 is around $60,000 per year, with the top 10% of the profession making more than $111,000 per year. (wgu.edu)
- UpCounsel accepts only the top 5 percent of lawyers on its site. (upcounsel.com)
- This field is expected to grow about 7% by 2028, a bit faster than the national average for job growth. (wgu.edu)
- Your choice in Step 5 may very likely be the same or similar to the alternative you placed at the top of your list at the end of Step 4. (umassd.edu)
- The profession is expected to grow 7% by 2028, a bit faster than the national average. (wgu.edu)
External Links
How To
How do I get my Six Sigma license?
Six Sigma is a tool for quality management to improve processes and increase efficiency. It is a method that enables companies to achieve consistent results with their operations. The name derives its meaning from the "sigmas" Greek word, which is composed of two letters that mean six. Motorola developed this process in 1986. Motorola recognized that they had to standardize their manufacturing processes to produce faster and more affordable products. There were many people doing the work and they had difficulty achieving consistency. To overcome this problem they turned to statistical tools such control charts and Pareto analyses. They would then apply these techniques to all aspects of their operation. This technique would enable them to make improvements in areas that needed it. When you are trying to obtain your Six Sigma certification, there are three steps. To determine whether you are qualified, the first step is to verify your eligibility. You will need classes to pass before you can begin taking tests. Once you pass those classes, the test will begin. You'll need to go back and review all the information you received in class. After that, you can take the test. You will be certified if you pass the test. And finally, you'll be able to add your certifications to your resume.