
You have come to the right spot if your search for a Portland-based waste management firm is over. You can choose from Kahut Waste Services, Heiberg Garbage, Sunset Garbage, and Waste Management. These companies can take care of your waste management needs. They can even recycle it for you. We'll explain all of the options available to you in this article.
Heiberg Garbage
Heiberg Garbage & Recycling, LLC, is a company that was established in 1967, in Portland's Sellwood/Moreland district. Marian and Vern Heiberg founded the company. Vern Heiberg was the one responsible for collecting and driving garbage. Marian was the bookkeeper and dealt with paperwork. In 1967, the company was able buy its first compactor truck and started providing collection services for the surrounding area.
Vern Heiberg began the company with a single truck. After two years running the route all by himself, he hired Adam Cooler to help with the heavy lifting. They now have 39 trucks and employ nearly fifty people. Vern still owns the business, but his kids now manage the day-today operations. The company also has 11 backup trucks that are kept in good shape in the garage. To maintain the trucks in good condition, the company employs an experienced mechanic.
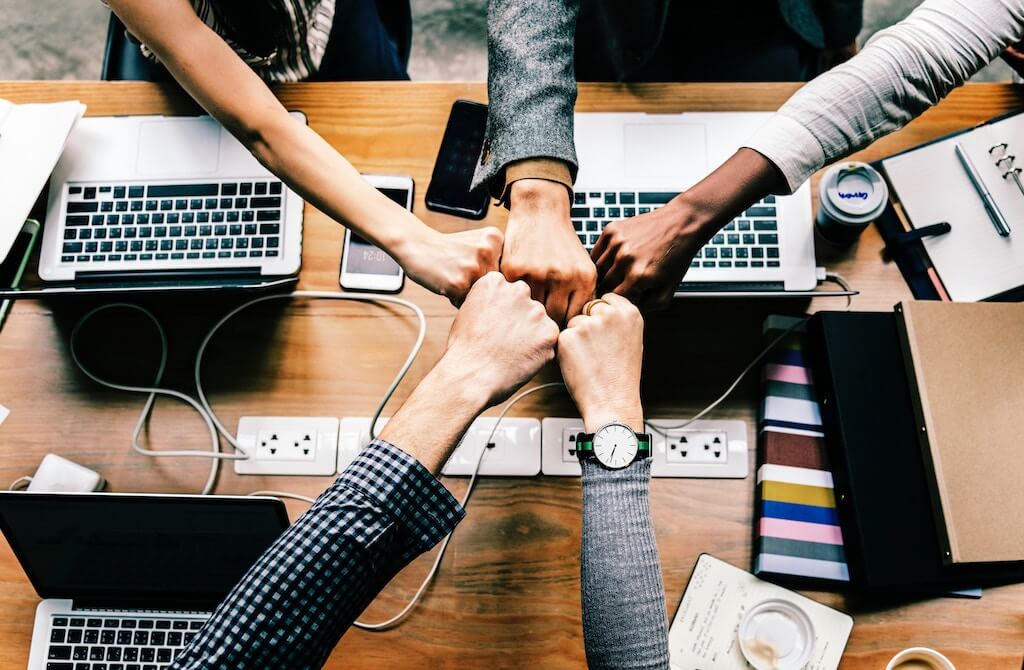
Kahut Waste Services
The Kahut family of businesses operates in the waste industry. They provide solid waste collection, recycling and materials recovery services for residents and businesses in Northwest Oregon. The company covers a large area of Oregon, including Portland and Canby. The company's professional staff is available to assist customers at all times of the day. For more information, visit the Kahut Waste Services site.
Hoodview Disposal and Recycling, Inc. and West Linn Refuse & Recycling, Inc. are owned by the Kahut family. They also hold solid waste collection franchises within the County. The Company's relationship to the County began 47 year ago when the Kahut Brothers purchased a Canby-based garbage collection service. They incorporated it as Canby Disposal Service. The family has been expanding its business in other areas, including Portland.
Sunset Garbage
Sunset Garbage, a family-owned franchise, offers residential waste management services within the Portland area. Founded in 1919 by John Guinazzo, the company has grown from a one-man route in the lower southeast to a franchise that now services the entire Clackamas County. The company is committed ensuring quality service and providing a safe work environment to its employees. These are just a few of the services offered by the company.
Sunset Garbage recycles to keep costs low. It encourages customers to put out their glass bins and recycling carts only when they are full. This ensures more efficient collections and costs are controlled. Customers will also be charged for filling incorrectly or damaging carts. Sunset Garbage asks customers to take their garbage out of the curbside after they have been collected. Sunset Garbage has a range of services available for both residential and commercial customers.
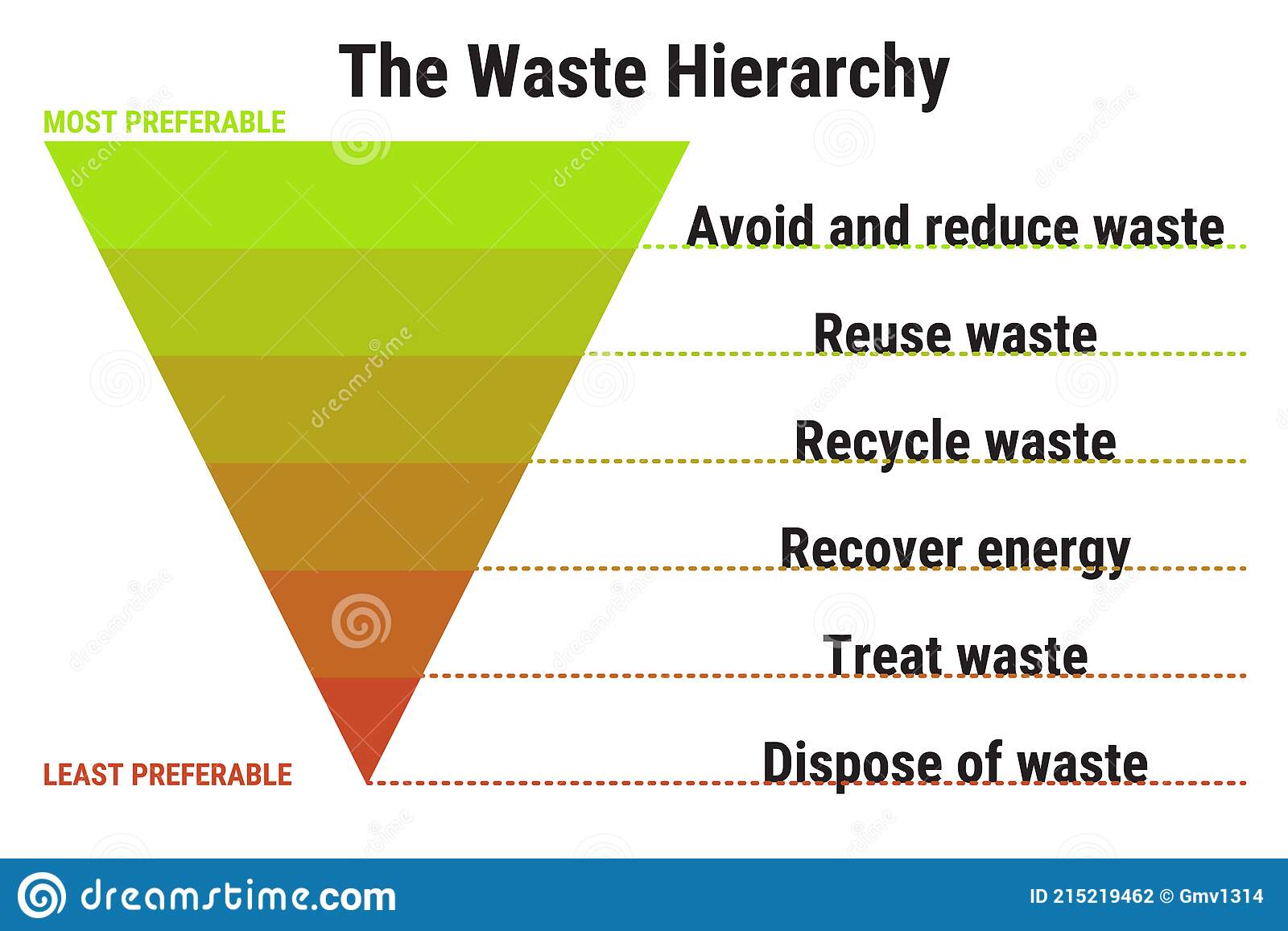
Waste Management
Waste Management can be counted on when it comes to disposing of your garbage. Waste Management offers a wide range of services including curbside pickup, recycling, disposal, and disposal. They offer life and medical insurance, as well as vision and vision insurance. Employees can take advantage of company-matched accounts for 401K and personal days. Waste Management's website has more information. It offers several online solutions, including traffic updates and reviews for local businesses.
You may be able to use their garbage and recycling services if you rent an apartment. Multifamily property owners provide this service to their tenants, and you should ask about it when you move in. For free recycling resources, contact the City of Portland. Donate reusable items at garage sales, donation centers and other events. You can also drop off recyclables at the city's drop-off location. These services are a great way of reducing garbage and saving the environment.
FAQ
What does "project management" mean?
It refers to the management of activities related to a project.
These include planning the scope and identifying the needs, creating the budget, organizing the team, scheduling the work and monitoring progress. Finally, we close down the project.
What is a basic management tool used in decision-making?
A decision matrix is an easy but powerful tool to aid managers in making informed decisions. It helps them to think strategically about all options.
A decision matrix is a way of representing alternatives as rows and columns. It is easy to see how each option affects the other options.
In this example, there are four possible options represented by boxes on the left-hand side of the matrix. Each box represents an option. The top row represents the current state of affairs, and the bottom row is indicative of what would happen in the event that nothing were done.
The middle column displays the impact of selecting Option 1. It would translate into an increase in sales from $2million to $3million.
The next two columns show the effects of choosing Options 2 and 3. These are positive changes - they increase sales by $1 million and $500 thousand respectively. However, these also involve negative consequences. Option 2 increases costs by $100 thousand, while Option 3 decreases profits to $200 thousand.
The final column shows the results for Option 4. This would result in a reduction of sales of $1 million.
The best part of using a decision-matrix is that it doesn't require you to know which numbers belong where. Simply look at the cells to instantly determine if one choice is better than the other.
This is because your matrix has already done the hard work. It is as simple a matter of comparing all the numbers in each cell.
Here's a sample of how you might use decision matrixes in your business.
You need to decide whether to invest in advertising. This will allow you to increase your revenue by $5000 per month. However, additional expenses of $10 000 per month will be incurred.
By looking at the cell just below "Advertising", the net result can be calculated as $15 thousand. Therefore, you should choose to invest in advertising since it is worth more than the cost involved.
Six Sigma is so well-known.
Six Sigma can be implemented quickly and produce impressive results. It can also be used to help companies identify and focus on the most important aspects of their business.
Statistics
- This field is expected to grow about 7% by 2028, a bit faster than the national average for job growth. (wgu.edu)
- Hire the top business lawyers and save up to 60% on legal fees (upcounsel.com)
- The average salary for financial advisors in 2021 is around $60,000 per year, with the top 10% of the profession making more than $111,000 per year. (wgu.edu)
- As of 2020, personal bankers or tellers make an average of $32,620 per year, according to the BLS. (wgu.edu)
- UpCounsel accepts only the top 5 percent of lawyers on its site. (upcounsel.com)
External Links
How To
How can Lean Manufacturing be done?
Lean Manufacturing methods are used to reduce waste through structured processes. They were created by Toyota Motor Corporation in Japan in the 1980s. It was designed to produce high-quality products at lower prices while maintaining their quality. Lean manufacturing seeks to eliminate unnecessary steps and activities in the production process. It is composed of five fundamental elements: continuous improvement; pull systems, continuous improvements, just-in–time, kaizen, continuous change, and 5S. Pull systems allow customers to get exactly what they want without having to do extra work. Continuous improvement means continuously improving on existing processes. Just-in–time refers when components or materials are delivered immediately to their intended destination. Kaizen is continuous improvement. This can be achieved by making small, incremental changes every day. The 5S acronym stands for sort in order, shine standardize and maintain. To achieve the best results, these five elements must be used together.
Lean Production System
Six key concepts form the foundation of the lean production system:
-
Flow: The goal is to move material and information as close as possible from customers.
-
Value stream mapping is the ability to divide a process into smaller tasks, and then create a flowchart that shows the entire process.
-
Five S’s - Sorted, In Order. Shine. Standardize. And Sustain.
-
Kanban – visual signals like colored tape, stickers or other visual cues are used to keep track inventory.
-
Theory of constraints: identify bottlenecks in your process and eliminate them using lean tools, such as kanban board.
-
Just-in-time delivery - Deliver components and materials right to your point of use.
-
Continuous improvement: Make incremental improvements to the process instead of overhauling it completely.