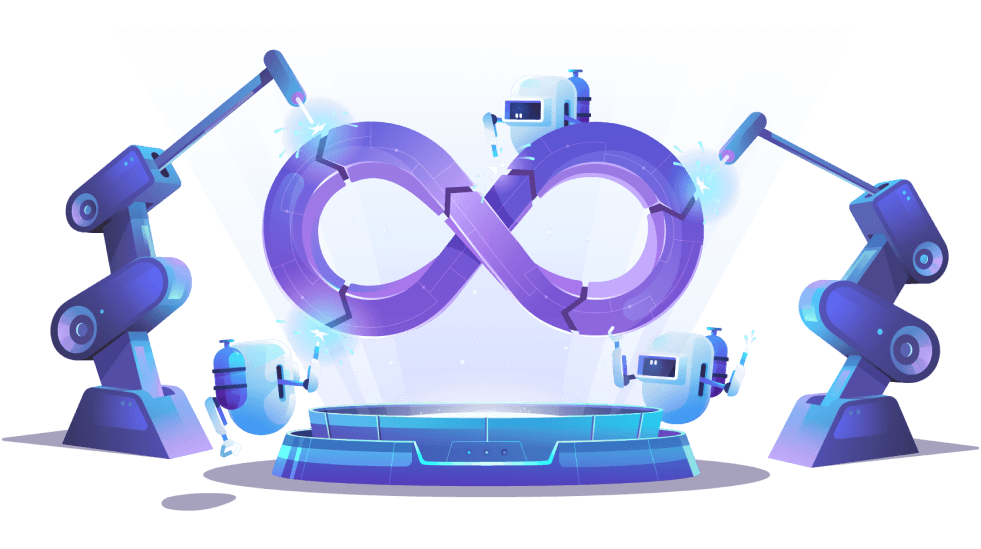
Strategic sourcing involves identifying and evaluating the best vendors for a given task. It involves many steps, including market research, benchmarking, evaluations, and finding the best partners to provide the greatest value. Not only is it important to determine the best vendor for each task, but strategic sourcing also considers return on investments at each step. This includes assessing the cost and time involved in setting up a new vendor as well as potential savings in the long-term.
Market research
Market research agencies unlock the potential of your organization by identifying new markets and demographics. They also help you develop concrete business strategies backed by data. These agencies perform different types of research, including primary research (focus groups), secondary research (review of published sources and identifying relevant publications), and data acquisition (data mining).
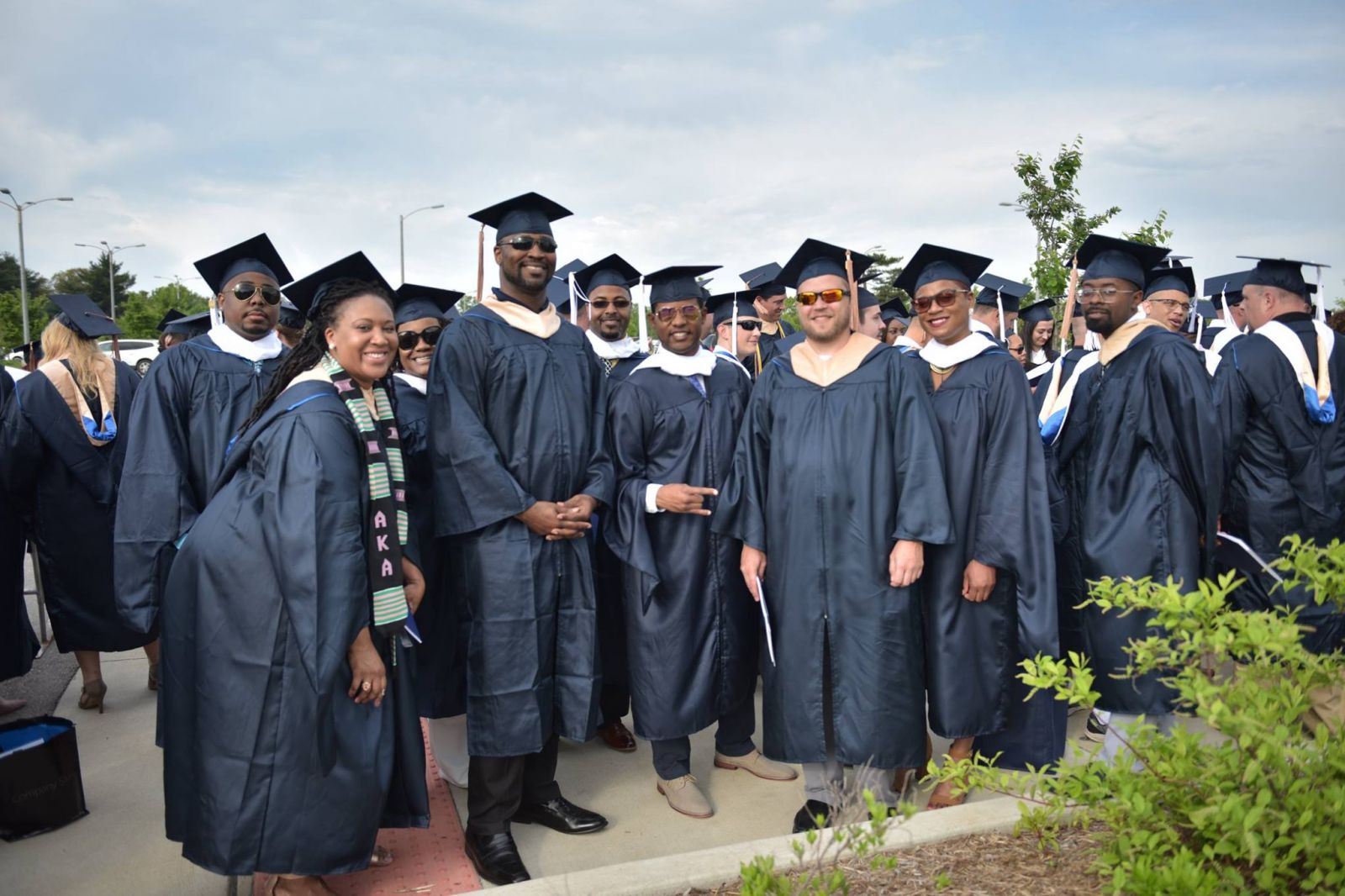
Forecasting
Forecasting is an important aspect of strategic sourcing. Forecasting allows businesses to predict demand and can reduce lead times. This can also lead to increased customer trust. Forecasting can help eliminate safety stock, which is surplus inventory kept to meet unforeseeable demand. This helps to free up storage space as well as save time.
Building partnerships
Strategic sourcing requires the creation of partnerships with suppliers capable of fulfilling a particular requirement. These partnerships must be developed through a collaborative process. It is essential to build trust and align with shared goals. A dedicated resource is required to ensure that successful partnerships lead to better business outcomes.
Recognizing the best partner
The strategic sourcing process starts with identifying the right partner. Before signing a strategic sourcing agreement, it is crucial to communicate with suppliers and learn about their capabilities. Once a strategic sourcing team has selected its ideal partner, it needs to communicate the next steps to its suppliers and implement their recommendations.
Analyse the cost
Strategic sourcing involves cost analysis. This allows companies to see the profit margins of their suppliers and helps them determine if they can cut costs by selecting a cheaper supplier. It can also be used for comparing prices of components and assemblies. The result can inform a procurement team on which components and assemblies to buy and which ones to manufacture.
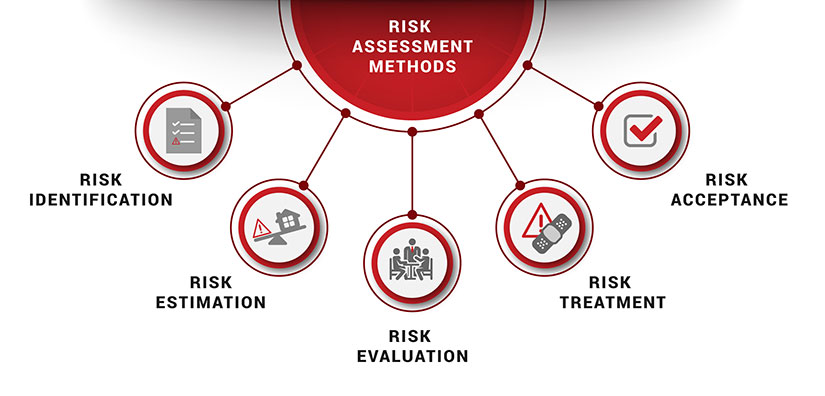
Technology for RFP
Strategic sourcing includes the use of RFP technology. This technology allows companies streamline their processes and to evaluate suppliers more efficiently. Companies can reduce time and save money by automating their supplier evaluations. An RFP software program, for example, can cut down on the time it takes shortlist suppliers. Companies can also create vendor profiles to keep track of changes and stay up to date with developments.
FAQ
What are some of the common mistakes made by managers?
Sometimes, managers make their job more difficult than it is.
They may not delegate enough responsibilities and not provide sufficient support.
Managers often lack the communication skills necessary to motivate and guide their teams.
Managers sometimes set unrealistic expectations of their teams.
Managers may attempt to solve all problems themselves, rather than delegating it to others.
How to effectively manage employees
The key to effective management of employees is ensuring their happiness and productivity.
This includes setting clear expectations for their behavior and tracking their performance.
Managers must be clear about their goals and those of their teams in order to succeed.
They should communicate clearly with employees. And they need to ensure that they reward good performance and discipline poor performers.
They must also keep track of the activities of their team. These include:
-
What was the result?
-
What was the work involved?
-
Who did it and why?
-
When it was done?
-
Why it was done?
This information can be used for monitoring performance and evaluating results.
How does Six Sigma function?
Six Sigma uses statistical analyses to locate problems, measure them, analyze root cause, fix problems and learn from the experience.
The first step in solving a problem is to identify it.
The data is then analyzed and collected to identify trends.
Next, corrective steps are taken to fix the problem.
Finally, the data are reanalyzed in order to determine if it has been resolved.
This cycle continues until there is a solution.
What are the four major functions of Management?
Management is responsible of planning, organizing, leading, and controlling people as well as resources. Management also involves setting goals and developing policies.
Management helps an organization achieve its objectives by providing direction, coordination, control, leadership, motivation, supervision, training, and evaluation.
These are the four major functions of management:
Planning - Planning refers to deciding what is needed.
Organizing - Organizing involves deciding how things should be done.
Directing – This means to get people to follow directions.
Controlling: Controlling refers to making sure that people do what they are supposed to.
What are the 3 basic management styles?
There are three main management styles: participative, laissez-faire and authoritarian. Each style has strengths and flaws. What style do you prefer? Why?
Authority - The leader is the one who sets the direction and expects everyone in the organization to follow it. This style works well if an organization is large and stable.
Laissez faire - Each individual can decide for himself/herself. This style works best when an organization is small and dynamic.
Participative - The leader listens to ideas and suggestions from everyone. This style is best for small organizations where everyone feels valued.
What is Six Sigma and how can it help you?
It's a strategy for quality improvement that emphasizes customer care and continuous learning. The objective is to eliminate all defects through statistical methods.
Motorola created Six Sigma as part of their efforts to improve manufacturing processes in 1986.
The idea spread quickly in the industry. Today many organizations use six-sigma techniques to improve product design.
What are the 5 management processes?
Planning, execution, monitoring and review are the five stages of any business.
Setting goals for the future requires planning. Planning involves defining your goals and how to get there.
Execution takes place when you actually implement the plans. These plans must be adhered to by everyone.
Monitoring is the act of monitoring your progress towards achieving your targets. Regular reviews of performance against budgets and targets should be part of this process.
Review events take place at each year's end. These reviews allow you to evaluate whether the year was successful. If not, then it may be possible to make adjustments in order to improve performance next time.
Evaluation takes place after the annual review. It helps identify which aspects worked well and which didn't. It also provides feedback regarding how people performed.
Statistics
- 100% of the courses are offered online, and no campus visits are required — a big time-saver for you. (online.uc.edu)
- This field is expected to grow about 7% by 2028, a bit faster than the national average for job growth. (wgu.edu)
- UpCounsel accepts only the top 5 percent of lawyers on its site. (upcounsel.com)
- As of 2020, personal bankers or tellers make an average of $32,620 per year, according to the BLS. (wgu.edu)
- The BLS says that financial services jobs like banking are expected to grow 4% by 2030, about as fast as the national average. (wgu.edu)
External Links
How To
How do I get my Six Sigma License?
Six Sigma can be used to improve quality and efficiency. It's a system that allows companies to get consistent results from operations. The name derives its meaning from the "sigmas" Greek word, which is composed of two letters that mean six. This process was developed at Motorola in 1986. Motorola recognized that they had to standardize their manufacturing processes to produce faster and more affordable products. There were many people doing the work and they had difficulty achieving consistency. They decided to use statistical tools like control charts and Pareto analysis to solve the problem. After this, they would apply these techniques to every part of the operation. They would then be able make improvements where needed. Three main steps are involved when you're trying to go through the whole process of getting your Six Sigma certification. To determine whether you are qualified, the first step is to verify your eligibility. You will need to complete some classes before you can start taking the tests. After you have passed the classes, you can start taking the exams. You'll want to study everything you learned during the class beforehand. Next, you'll be ready for the test. If you pass, then you will become certified. Final, your certifications can be added to you resume.