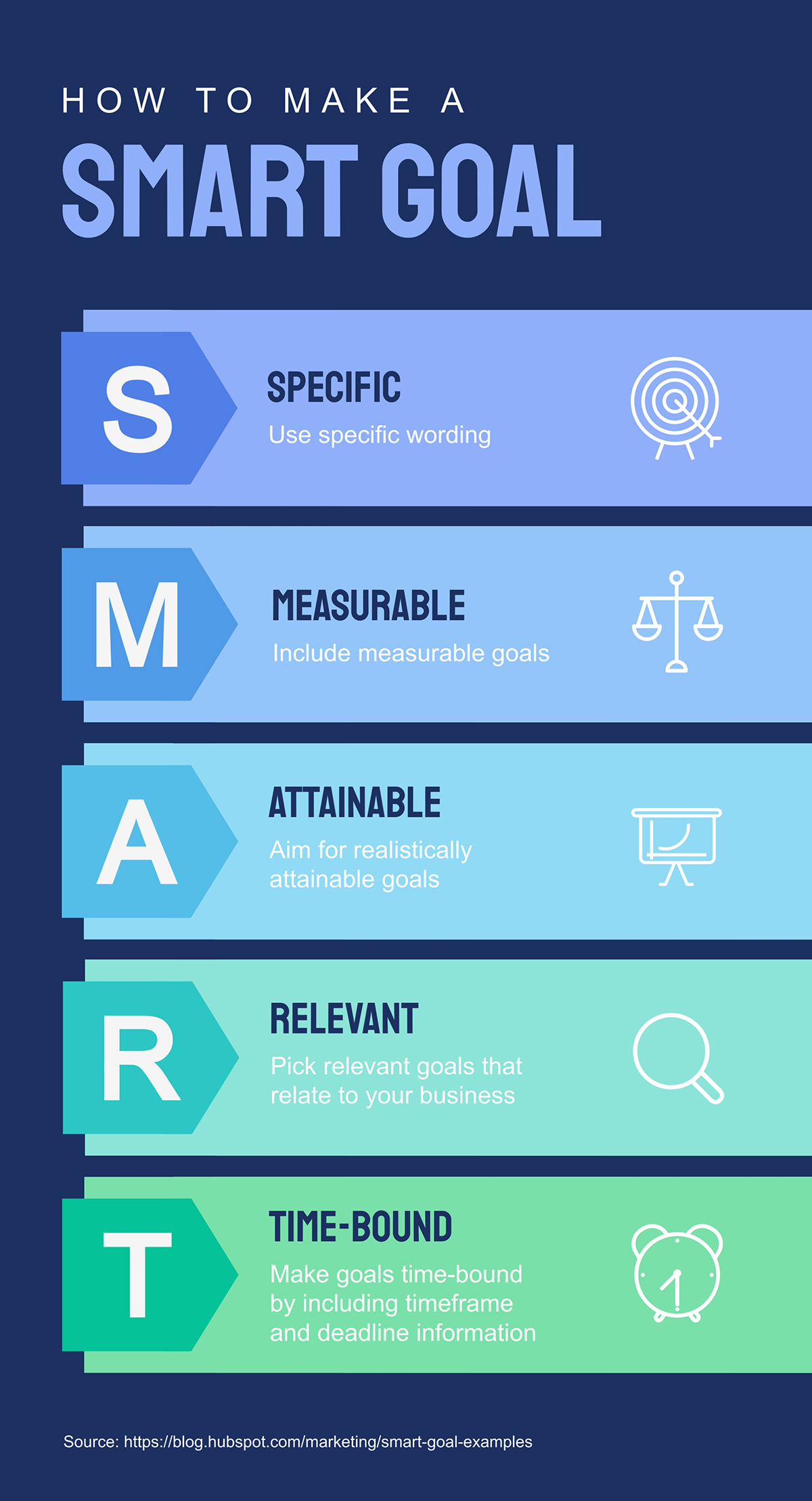
Becoming a PMI Member has many advantages. Among them is the ability to access an extensive knowledge base. A set of international standards ensures that users are operating within the guidelines. You also have the opportunity to volunteer and receive free PDUs. PMI members have the chance to give back both to their professions and to society. A member dashboard displays the most recent year of membership.
Education and training opportunities
The Project Management Institute (PMI) offers a wide range of education and training opportunities for its members. PMI certification demonstrates that you are knowledgeable about project management principles. Additionally, members of the association can enjoy lower certification examination fees. They can also use preparatory materials from the PMI and workshops from other component organizations.
You should take an online course if you want to become a PMP certified. These courses will give you a solid foundation in project management concepts and help you prepare for the exam. They will help you earn PDUs towards achieving your certification. PMI SeminarsWorld(tm), which allows you to attend PMI seminars, is also available. Additionally, there are also e-Symposia available to help you earn PDUs toward your PMP certification.

Global Conference events
PMI members are eligible for discounts on courses and certification exams. The organization also offers members free PDUs to maintain certifications. Additionally, the organization provides members with discounts on events and on-demand webinars. Members can register for premium virtual events free of charge and receive a 50% discount when they purchase three premium webinars.
These conferences are great opportunities to network with project managers. Global Conference brings together project management professionals from all corners of the globe. However, many local chapters also host conferences. These events provide a great networking opportunity for project managers from around the world and a chance to learn about how to improve their skills.
Access to the job portal
PMI members are able to access a job platform that provides the latest job opportunities in the sector. The database, which is continuously updated, is sourced from public job listings and solicitations for PM-related jobs. Access to this database is only available to members, who can also register as members. Membership provides you with more opportunities for career advancement and discounts on products/services.
PMI members have access to a huge database of career resources. This database features a Career Headquarter and Communities of Practice, where members can learn how to build a strong resume, acquire new skills, and stay updated on current trends. Members can also upload their resumes in the job portal. It also features a job-search tool that helps members search for work. PMI members also receive PM Network and PMI Today, the PMI magazine, for free each month.
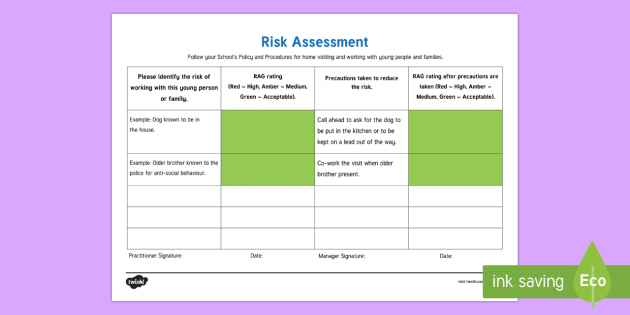
Certification fees
The cost of certification is affected by many factors. The cost of a classroom-based course may include the fees paid to the training provider, exam costs, and time spent in training. Alternatively, you can choose to take a self-paced online course. This option is cheaper and offers many benefits including time management. This option is flexible and available 24 hours a day. It's also easier than taking a class.
PMI offers discounts for its members. A member can get a $60 discount on a certification exam every three years. If you aren't a member, you will have to pay $129 annually. There are many levels to PMP membership if you are interested in becoming one. A basic membership is free and a higher-level membership costs $129.
FAQ
What are the five management process?
The five stages of a business include planning, execution (monitoring), review, evaluation, and review.
Planning involves setting goals for the future. Planning involves defining your goals and how to get there.
Execution takes place when you actually implement the plans. You need to make sure they're followed by everyone involved.
Monitoring is a way to track progress towards your objectives. Regular reviews of performance against budgets and targets should be part of this process.
At the end of every year, reviews take place. They give you an opportunity to review the year and assess how it went. If not, changes may be made to improve the performance next time around.
After the annual review, evaluation takes place. It helps identify what worked well and what didn't. It also provides feedback regarding how people performed.
Why is project management important for companies?
Project management techniques are used in order to ensure projects run smoothly, and that deadlines are met.
This is because most businesses rely heavily on project work to produce goods and services.
These projects are essential for companies.
Companies could lose their time, reputation, and money without effective project management.
What are the steps to take in order to make a management decision?
The decision-making process of managers is complicated and multifaceted. It involves many elements, including analysis, strategy. planning. implementation. measurement. evaluation. feedback.
Remember that people are humans just like you, and will make mistakes. This is the key to managing them. There is always room to improve, especially if your first priority is to yourself.
This video shows you how management makes decisions. We will explain the importance of different types decisions and how every manager can make them. These topics are covered in this course:
What can a manager do to improve his/her management skillset?
By practicing good management skills at all times.
Managers should monitor the performance and progress of their subordinates.
You should immediately take action if you see that your subordinate is not performing as well as you would like.
You must be able to spot what is lacking and how you can improve it.
What is TQM?
When manufacturing companies realized that price was not enough to compete, the industrial revolution brought about the quality movement. To remain competitive, they had to improve quality as well as efficiency.
In response to this need for improvement, management developed Total Quality Management (TQM), which focused on improving all aspects of an organization's performance. It included continuous improvement processes, employee involvement, and customer satisfaction.
What are some of the common mistakes made by managers?
Sometimes, managers make their job more difficult than it is.
They may not be able to delegate enough responsibility to staff or provide adequate support.
Additionally, many managers lack communication skills that are necessary to motivate and direct their teams.
Managers sometimes set unrealistic expectations of their teams.
Managers may attempt to solve all problems themselves, rather than delegating it to others.
What is Six Sigma?
Six Sigma uses statistical analyses to locate problems, measure them, analyze root cause, fix problems and learn from the experience.
First, identify the problem.
The data is then analyzed and collected to identify trends.
The problem can then be fixed by taking corrective measures.
Finally, data is reanalyzed to determine whether the problem has been eliminated.
This cycle continues until the problem is solved.
Statistics
- Your choice in Step 5 may very likely be the same or similar to the alternative you placed at the top of your list at the end of Step 4. (umassd.edu)
- 100% of the courses are offered online, and no campus visits are required — a big time-saver for you. (online.uc.edu)
- Hire the top business lawyers and save up to 60% on legal fees (upcounsel.com)
- UpCounsel accepts only the top 5 percent of lawyers on its site. (upcounsel.com)
- As of 2020, personal bankers or tellers make an average of $32,620 per year, according to the BLS. (wgu.edu)
External Links
How To
How can you implement the Kaizen technique?
Kaizen means continuous improvement. Kaizen is a Japanese concept that encourages constant improvement by small incremental changes. It's where people work together in order to improve their processes constantly.
Kaizen is one method that Lean Manufacturing uses to its greatest advantage. This concept requires employees to identify and solve problems during manufacturing before they become major issues. This way, the quality of products increases, and the cost decreases.
The main idea behind kaizen is to make every worker aware of what happens around him/her. If something is wrong, it should be corrected immediately so that no problem occurs. If someone is aware of a problem at work, he/she should inform his/her manager immediately.
There are some basic principles that we follow when doing kaizen. Start with the end product, and then move to the beginning. For example, if we want to improve our factory, we first fix the machines that produce the final product. Then, we fix the machines that produce components and then the ones that produce raw materials. We then fix the workers that work with those machines.
This is why it's called "kaizen" because it works step-by-step to improve everything. After we're done with the factory, it's time to go back and fix the problem.
To implement kaizen in your business, you need to find out how to measure its effectiveness. There are several ways that you can tell if your kaizen system is working. Another method is to see how many defects are found on the products. Another method is to determine how much productivity has improved since the implementation of kaizen.
You can also find out if kaizen works by asking yourself why you decided to implement it. It was because of the law, or simply because you wanted to save some money. You really believed it would make you successful?
Congratulations if you answered "yes" to any of the questions. You are ready to start kaizen.