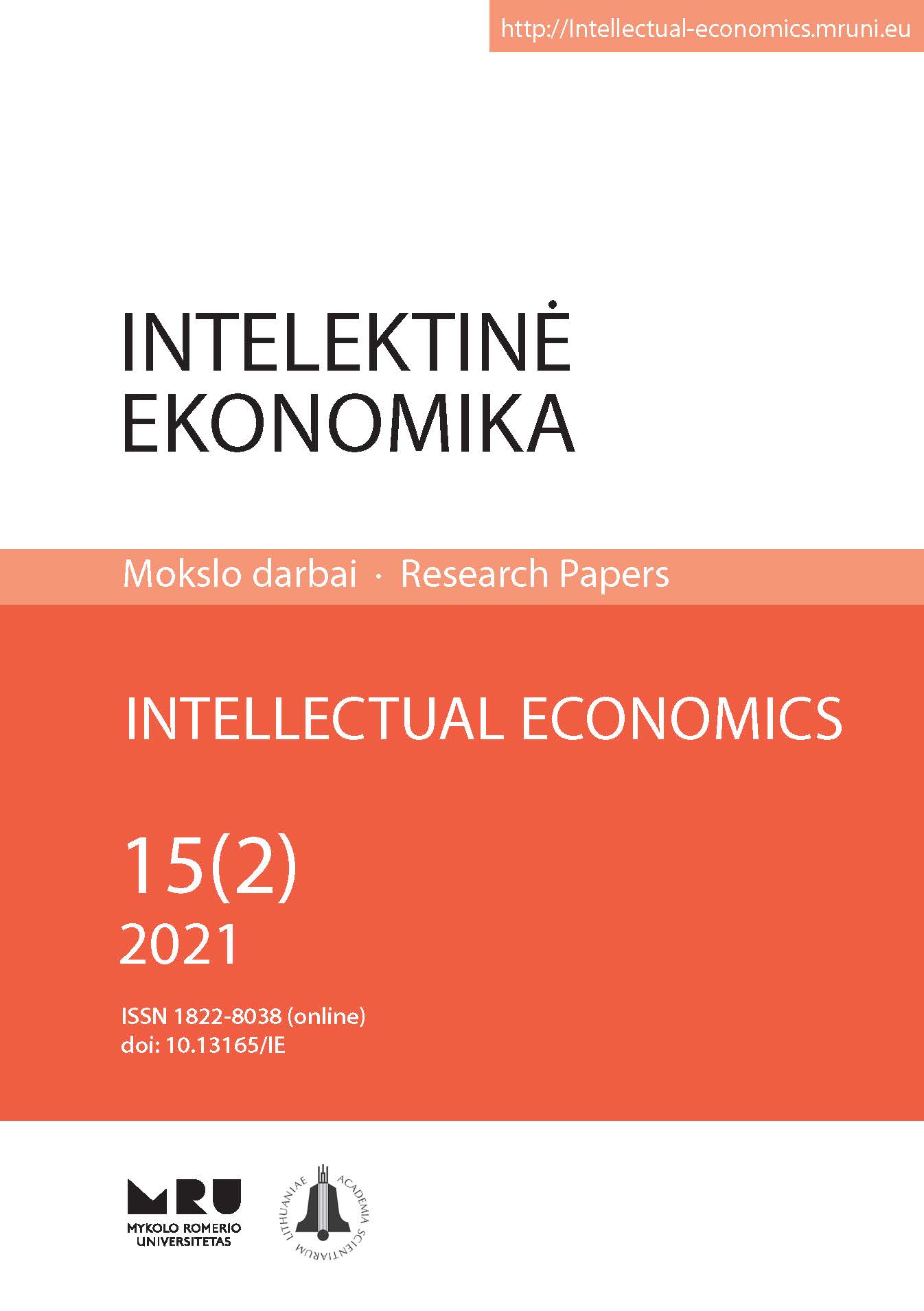
The success rate of corporate change management initiatives is very low. Even though scholars and consultants are better at understanding the phenomenon, new studies have shown that nearly three quarters (75%) of all change efforts do not deliver the expected results. These transformations are often abandoned. Here are some methods to improve the management of change.
Lessons from ASDA’s Driving Test
ASDA's experience is a great example of the importance of evolution and experimentation in managing change. ASDA launched an experimental store. It later expanded it to three more stores that were all declared to be risk-free. This case study shows that the driving force of ASDA's retail strategy, organizational structure, management team and retail proposition was redesigned. Managers were encouraged to experiment with layout, product ranges, and roles. It was an extremely successful strategy.
ASDA's top executives were given stock options linked to the company’s value. This was a great incentive for them and helped drive rapid company transformation. In addition to executives, the company's stock-ownership plan provided variable compensation based on store-level records and corporate performance. Despite the many challenges faced, the resultant culture of trusting and openness was a great success.
There are many ways to improve the management of change
HR professionals need to ensure the change is implemented smoothly and effectively, in addition to leading it. They will plan and communicate the key roles, key dates, and track results. They must listen to employees and adjust plans as required. HR professionals can support the process of change management through education and technology. The following are some ways to improve change management HR in your company. These tips will help you make your change management process more efficient.
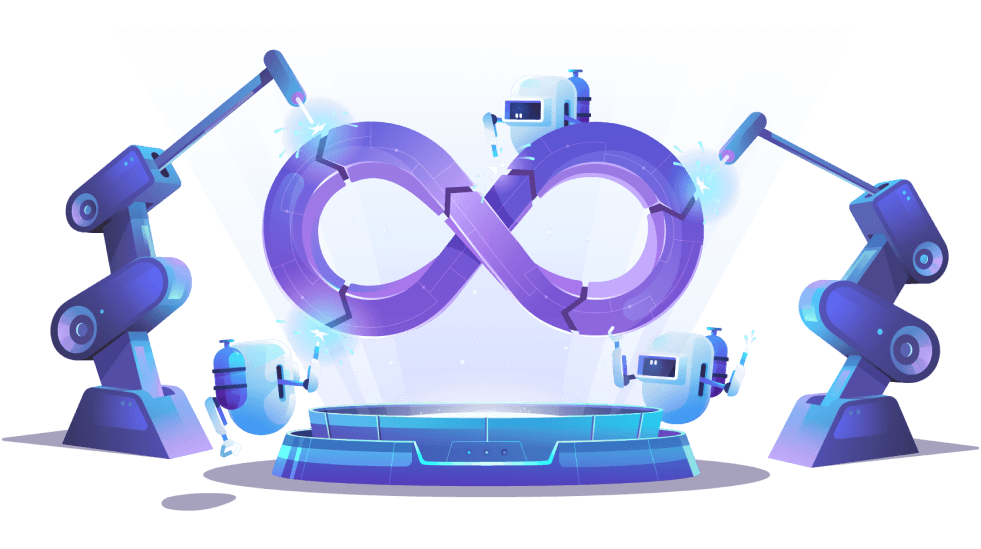
Identify those employees who are affected. Employees want to take part in the process. To receive feedback from employees, a dedicated channel should be created for this purpose. Employee engagement is important. Managers should be trained to make better decisions about the changes. Managers can also benefit from the information and training they receive on the changes. Include all employees in the change process, as well as managers, to build a positive culture. Encourage and recognize their valuable input.
FAQ
What is a management tool to help with decision-making?
A decision matrix can be a simple, but effective tool to assist managers in making decisions. They can think about all options and make informed decisions.
A decision matrix can be used to show alternative options as rows or columns. This allows one to see how each alternative impacts other options.
In this example, we have four possible alternatives represented by the boxes on the left side of the matrix. Each box represents a different option. The top row shows the status quo (the current situation), and the bottom row shows what would happen if nothing was done at all.
The effect of selecting Option 1 is shown in the middle column. In this case, it would mean increasing sales from $2 million to $3 million.
These are the results of selecting Options 2 or 3. These are positive changes - they increase sales by $1 million and $500 thousand respectively. These positive changes have their downsides. Option 2 can increase costs by $100 million, while Option 3 can reduce profits by $200,000.
The last column displays the results of selecting Option 4. This means that sales will decrease by $1 million.
The best thing about a decision matrix is the fact that you don't have to remember which numbers go with what. The best thing about a decision matrix is that you can simply look at the cells, and immediately know whether one option is better or not.
The matrix already does all the work. It is as simple as comparing the numbers within the relevant cells.
Here's an example showing how you might use a Decision Matrix in your business.
It is up to you to decide whether to spend more money on advertising. By doing so, you can increase your revenue by $5 000 per month. But, you will also incur additional expenses of $10 thousand per month.
Look at the cell immediately below the one that states "Advertising" to calculate the net investment in advertising. It's $15,000. Therefore, you should choose to invest in advertising since it is worth more than the cost involved.
What are the key management skills?
Any business owner needs to be able to manage people, finances, resources and time. They are the ability to manage people and finances, space, money, and other factors.
These skills are necessary for setting goals and objectives as well as planning strategies, leading groups, motivating employees and solving problems.
As you can see, there are many managerial responsibilities!
What are some common mistakes managers make when managing people?
Sometimes managers make it harder for their employees than is necessary.
They may not delegate enough responsibilities and not provide sufficient support.
Managers often lack the communication skills necessary to motivate and guide their teams.
Managers can set unrealistic expectations for their employees.
Managers might try to solve every problem by themselves rather than delegating the responsibility.
What are the steps involved in making a decision in management?
Managers have to make complex decisions. It involves many factors, including but not limited to analysis, strategy, planning, implementation, measurement, evaluation, feedback, etc.
When managing people, the most important thing to remember is that they are just human beings like you and make mistakes. You are always capable of improving yourself, and there's always room for improvement.
This video will explain how decision-making works in Management. We discuss different types of decisions as well as why they are important and how managers can navigate them. The following topics will be covered:
Statistics
- This field is expected to grow about 7% by 2028, a bit faster than the national average for job growth. (wgu.edu)
- As of 2020, personal bankers or tellers make an average of $32,620 per year, according to the BLS. (wgu.edu)
- Our program is 100% engineered for your success. (online.uc.edu)
- The BLS says that financial services jobs like banking are expected to grow 4% by 2030, about as fast as the national average. (wgu.edu)
- UpCounsel accepts only the top 5 percent of lawyers on its site. (upcounsel.com)
External Links
How To
What is Lean Manufacturing?
Lean Manufacturing uses structured methods to reduce waste, increase efficiency and reduce waste. They were created in Japan by Toyota Motor Corporation during the 1980s. The goal was to produce quality products at lower cost. Lean manufacturing seeks to eliminate unnecessary steps and activities in the production process. It consists of five basic elements: pull systems, continuous improvement, just-in-time, kaizen (continuous change), and 5S. Pull systems involve producing only what the customer wants without any extra work. Continuous improvement means continuously improving on existing processes. Just-intime refers the time components and materials arrive at the exact place where they are needed. Kaizen refers to continuous improvement. It is achieved through small changes that are made continuously. Five-S stands for sort. It is also the acronym for shine, standardize (standardize), and sustain. To achieve the best results, these five elements must be used together.
Lean Production System
Six key concepts form the foundation of the lean production system:
-
Flow is about moving material and information as near as customers can.
-
Value stream mapping is the ability to divide a process into smaller tasks, and then create a flowchart that shows the entire process.
-
Five S’s - Sorted, In Order. Shine. Standardize. And Sustain.
-
Kanban - use visual signals such as colored tape, stickers, or other visual cues to keep track of inventory;
-
Theory of Constraints - Identify bottlenecks in the process, and eliminate them using lean tools such kanban boards.
-
Just-in-time delivery - Deliver components and materials right to your point of use.
-
Continuous improvement is making incremental improvements to your process, rather than trying to overhaul it all at once.