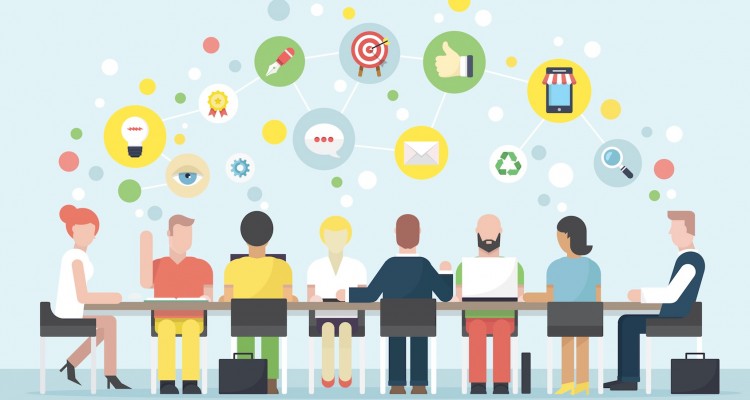
If you are interested, Primavera training courses may be for you. Primavera is a well-known project management tool that professionals have used for many years. It can be used to plan and schedule your projects. It includes many useful features, such as a large collection of templates.
Software to manage projects
Primavera project management software integrates risk analysis, opportunity management and collaboration. It also has control capabilities. It integrates with other enterprise software. Primavera is designed for large organizations that manage multiple projects and resources. It offers several other features, like resource and cost management.
Primavera P6 project management software offers powerful scheduling capabilities. It's powerful scheduling features let users attach resources and critical path items. Users can also compare planned costs with actual costs. This software will enable users to identify opportunities for cost savings or quality improvements.
Scheduling tool
This course introduces Primavera P6’s scheduling tool. The training covers how to use the scheduling tool for Primavera P6 and how you can create a project development plan. It also covers a practical approach to analyzing project data. All project staff, including programmers, planners, and project managers, will benefit from the course.
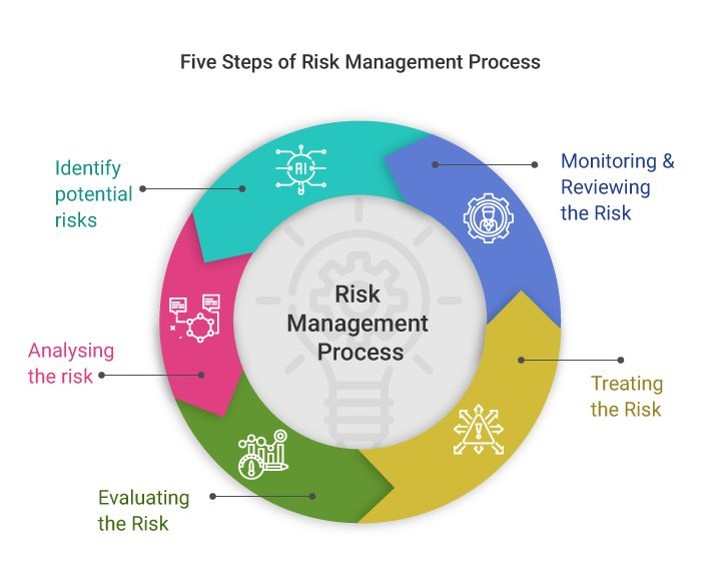
Primavera P6 is an integral part of training. This tool will save you time and help improve the performance of your schedule. It will also allow you to make detailed schedules. Online training is available. It includes practical examples and real-world case studies. You can complete the training in as little as six weeks. Each session takes three to four hours.
FAQ
What is the main difference between Six Sigma Six Sigma TQM and Six Sigma Six Sigma?
The major difference between the two tools for quality management is that six Sigma focuses on eliminating defect while total quality control (TQM), on improving processes and decreasing costs.
Six Sigma stands for continuous improvement. It emphasizes the elimination or minimization of defects through statistical methods such control charts and p charts.
This method attempts to reduce variations in product output. This is done by identifying and correcting the root causes of problems.
Total quality management refers to the monitoring and measurement of all aspects in an organization. It also includes the training of employees to improve performance.
It is commonly used as a strategy for increasing productivity.
What are the 4 main functions of management?
Management is responsible for planning, organizing, directing, and controlling people and resources. It includes creating policies and procedures, as well setting goals.
Management aids an organization in reaching its goals by providing direction and coordination, control, leadership motivation, supervision, training, evaluation, and leadership.
These are the four major functions of management:
Planning – Planning involves deciding what needs to happen.
Organizing is the act of deciding how things should go.
Directing – This means to get people to follow directions.
Controlling – Controlling is the process of ensuring that tasks are completed according to plan.
What are the five management process?
These five stages are: planning, execution monitoring, review and evaluation.
Planning is about setting goals for your future. It involves setting goals and making plans.
Execution happens when you actually do the plan. It is important to ensure that everyone follows the plans.
Monitoring is the act of monitoring your progress towards achieving your targets. Monitoring should include regular reviews of performance against goals and budgets.
Every year, there are reviews. They allow for an assessment of whether all went well throughout the year. If not, then it may be possible to make adjustments in order to improve performance next time.
Following the annual review, evaluation is done. It helps you identify the successes and failures. It also gives feedback on how well people did.
What is Six Sigma, exactly?
It's an approach to quality improvement that emphasizes customer service and continuous learning. The goal is to eradicate defects through statistical techniques.
Motorola's 1986 efforts to improve manufacturing process efficiency led to the creation of Six Sigma.
The idea spread quickly in the industry. Today many organizations use six-sigma techniques to improve product design.
How can a manager improve his/her managerial skills?
It is important to have good management skills.
Managers need to monitor their subordinates' performance.
It is important to take immediate action if your subordinate doesn't perform as expected.
It is important to be able identify areas that need improvement and what can be done to improve them.
What is the meaning of "project management?"
We mean managing the activities involved in carrying out a project.
We help you define the scope of your project, identify the requirements, prepare the budget, organize the team, plan the work, monitor progress and evaluate the results before closing down the project.
Statistics
- Hire the top business lawyers and save up to 60% on legal fees (upcounsel.com)
- Our program is 100% engineered for your success. (online.uc.edu)
- The BLS says that financial services jobs like banking are expected to grow 4% by 2030, about as fast as the national average. (wgu.edu)
- As of 2020, personal bankers or tellers make an average of $32,620 per year, according to the BLS. (wgu.edu)
- The average salary for financial advisors in 2021 is around $60,000 per year, with the top 10% of the profession making more than $111,000 per year. (wgu.edu)
External Links
How To
What is Lean Manufacturing?
Lean Manufacturing is a method to reduce waste and increase efficiency using structured methods. They were created by Toyota Motor Corporation in Japan in the 1980s. It was designed to produce high-quality products at lower prices while maintaining their quality. Lean manufacturing focuses on eliminating unnecessary steps and activities from the production process. It is made up of five elements: continuous improvement, continuous improvement, just in-time, continuous change, and 5S. Pull systems involve producing only what the customer wants without any extra work. Continuous improvement refers to continuously improving existing processes. Just-in-time is when components and other materials are delivered at their destination in a timely manner. Kaizen means continuous improvement, which is achieved by implementing small changes continuously. The 5S acronym stands for sort in order, shine standardize and maintain. These five elements are combined to give you the best possible results.
Lean Production System
Six key concepts underlie the lean production system.
-
Flow: The goal is to move material and information as close as possible from customers.
-
Value stream mapping is the ability to divide a process into smaller tasks, and then create a flowchart that shows the entire process.
-
Five S's: Sort, Shine Standardize, Sustain, Set In Order, Shine and Shine
-
Kanban - use visual signals such as colored tape, stickers, or other visual cues to keep track of inventory;
-
Theory of constraints - identify bottlenecks during the process and eliminate them with lean tools like Kanban boards.
-
Just-in time - Get components and materials delivered right at the point of usage;
-
Continuous improvement is making incremental improvements to your process, rather than trying to overhaul it all at once.