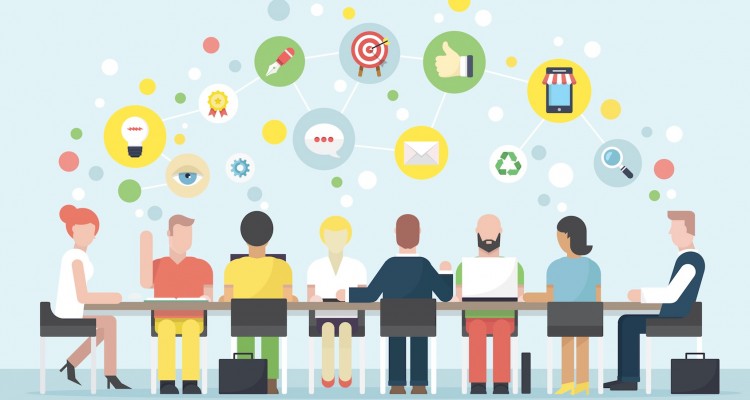
A supply chain framework is a process to help companies make better business decisions. Communication is a crucial component. The five steps that make up the rational process are: identifying the problem; analyzing potential solutions; gathering data; analyzing possible outcomes; deciding on the best solution.
Inventory is key to supply chain success
Management of inventory is a key function of manufacturing firms. This allows the production of the right product at just the right time and place. This function is more important in a global market where products can be manufactured anywhere. It is crucial to a company’s efficiency as well as responsiveness.
You need to be able anticipate customer needs, and to adapt to changing conditions. Companies need to share data about production schedules and inventory levels with their partners. This allows them quickly respond to market changes. This dynamic market requires inventory management to make sure companies are able to meet customer demands.
Collaboration and communication are crucial.
Collaboration and communication are crucial to supply chain decision making in today's fast-paced environment. These relationships enable companies to better respond to changing market demands and offer competitive differentiation. Collaboration can help organisations develop new skills, access new resources and stay in line with their peers. It can also be a way for businesses to grow their customer base.
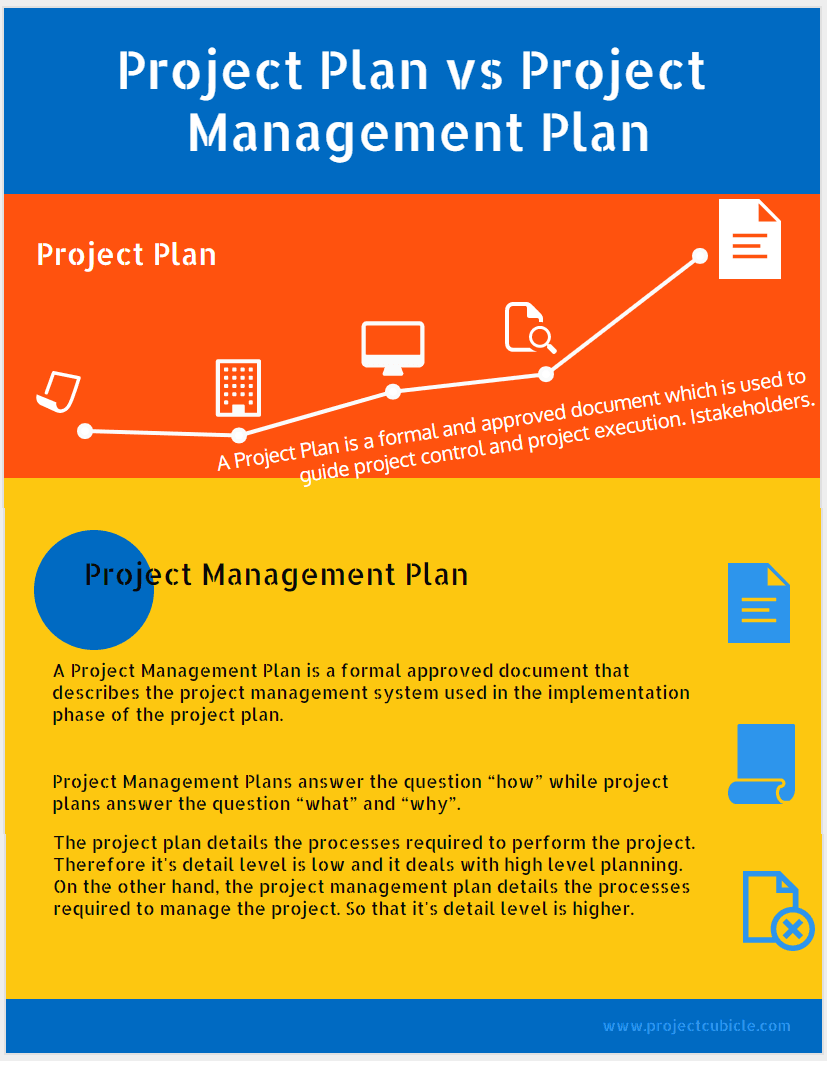
Creating successful collaborative relationships requires high levels of commitment and trust. A culture that is compatible with collaboration must be maintained by organisations.
Financial attributes
Supply chain decision making should not be limited to economic factors. It should consider financial and other environmental factors when deciding on supply chain decisions. It is crucial to improve cash flow across the supply chain. These attributes will affect the level and quality of working capital both at suppliers and buyers. This is significant because cash flow directly relates to suppliers' level of finance leverage, capital access, and financial stability. SCF should be improved by financial attributes. Financial attributes also play a crucial role in investment in green technology and environmental policy. Social values are also directly connected to financial and environmental policy.
This framework is a decision-making tool for supply chains and interlinks different components. It also addresses open research questions. The framework is useful across industries and sector.
Environmental attributes
A growing trend is to incorporate environmental attributes into supply chain decision-making frameworks. This is due to a greater awareness of environmental issues. Many companies adopt environmental performance measures for a variety reasons. Although environmental performance measurement is a complicated issue, both the parties and the environment can reap substantial benefits.
These are financial, environmental, and social criteria. This framework will help companies select the most eco-friendly suppliers to their businesses. It should also be useful in helping them adopt environmental practices within their own companies.
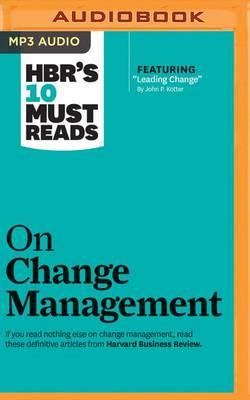
Prioritizing
The key aspect of supply chain decision-making is demand prioritization. It is important to identify the most profitable demand, and then allocate resources to support it. In some cases this could mean delaying orders and offering a substitute product. This will help to manage risk. The entire process should be documented and communicated with all levels of management. While the supply should be able to input costs, the demand should have all the information they need about the customer's needs and their sales goals.
Next, you need to find opportunities to acquire capacity, raw materials, or labor pools. A company may want to explore opportunities to acquire raw materials from alternative sources at lower piece prices and shorter lead times. But, this could impact margin and working capital. In the same way, expanding operations may be necessary during off-peak times or to secure additional transportation capacity.
FAQ
What are the steps in the decision-making process in management?
The decision-making process of managers is complicated and multifaceted. It involves many elements, including analysis, strategy. planning. implementation. measurement. evaluation. feedback.
When managing people, the most important thing to remember is that they are just human beings like you and make mistakes. There is always room to improve, especially if your first priority is to yourself.
In this video, we explain what the decision-making process looks like in Management. We will discuss the various types of decisions, and why they are so important. Every manager should be able to make them. The following topics will be covered.
What is a simple management tool that aids in decision-making and decision making?
The decision matrix is a powerful tool that managers can use to help them make decisions. It helps them think systematically about all the options available to them.
A decision matrix can be used to show alternative options as rows or columns. This makes it easy for you to see how each option affects other options.
We have four options in this example. They are represented by the boxes to the left of the matrix. Each box represents an alternative. The top row depicts the current status quo, while the bottom row represents what would happen if no action was taken.
The effect of choosing Option 1 can be seen in column middle. It would increase sales by $2 million to 3 million in this instance.
The results of choosing Option 2 and 3 can be seen in the columns below. These positive changes result in increased sales of $1 million and $500,000. These positive changes have their downsides. For instance, Option 2 increases cost by $100 thousand while Option 3 reduces profits by $200 thousand.
The final column shows results of choosing Option 4. This will result in sales falling by $1,000,000
The best thing about using a decision matrix is that you don't need to remember which numbers go where. The best thing about a decision matrix is that you can simply look at the cells, and immediately know whether one option is better or not.
The matrix has already done all of the work. It is as simple as comparing the numbers within the relevant cells.
Here is an example how you might use the decision matrix in your company.
It is up to you to decide whether to spend more money on advertising. You'll be able increase your monthly revenue by $5000 if you do. You will still have to pay $10000 per month in additional expenses.
You can calculate the net result of investing in advertising by looking at the cell directly below the one that says "Advertising." That number is $15 thousand. Advertising is worth more than its cost.
Why does it sometimes seem so difficult to make good business decisions?
Complex systems are often complex and have many moving parts. Their leaders must manage multiple priorities, as well as dealing with uncertainty.
Understanding the impact of these factors on the system is crucial to making sound decisions.
You must first consider what each piece of the system does and why. Then, you need to think about how these pieces interact with one another.
Ask yourself if there are hidden assumptions that have influenced your behavior. If not, you might want to revisit them.
Asking for assistance from someone else is a good idea if you are still having trouble. You might find their perspective is different from yours and they may have insight that can help you find the solution.
Statistics
- 100% of the courses are offered online, and no campus visits are required — a big time-saver for you. (online.uc.edu)
- The profession is expected to grow 7% by 2028, a bit faster than the national average. (wgu.edu)
- Hire the top business lawyers and save up to 60% on legal fees (upcounsel.com)
- The BLS says that financial services jobs like banking are expected to grow 4% by 2030, about as fast as the national average. (wgu.edu)
- This field is expected to grow about 7% by 2028, a bit faster than the national average for job growth. (wgu.edu)
External Links
How To
How is Lean Manufacturing done?
Lean Manufacturing techniques are used to reduce waste while increasing efficiency by using structured methods. They were developed in Japan by Toyota Motor Corporation (in the 1980s). The goal was to produce quality products at lower cost. Lean manufacturing eliminates unnecessary steps and activities from a production process. It is composed of five fundamental elements: continuous improvement; pull systems, continuous improvements, just-in–time, kaizen, continuous change, and 5S. The production of only what the customer needs without extra work is called pull systems. Continuous improvement refers to continuously improving existing processes. Just-intime refers the time components and materials arrive at the exact place where they are needed. Kaizen means continuous improvement, which is achieved by implementing small changes continuously. Last but not least, 5S is for sort. These five elements are combined to give you the best possible results.
Lean Production System
The lean production system is based on six key concepts:
-
Flow - focuses on moving information and materials as close to customers as possible.
-
Value stream mapping is the ability to divide a process into smaller tasks, and then create a flowchart that shows the entire process.
-
Five S's: Sort, Shine Standardize, Sustain, Set In Order, Shine and Shine
-
Kanban - use visual signals such as colored tape, stickers, or other visual cues to keep track of inventory;
-
Theory of constraints - identify bottlenecks in the process and eliminate them using lean tools like kanban boards;
-
Just-in-time delivery - Deliver components and materials right to your point of use.
-
Continuous improvement - incremental improvements are made to the process, not a complete overhaul.