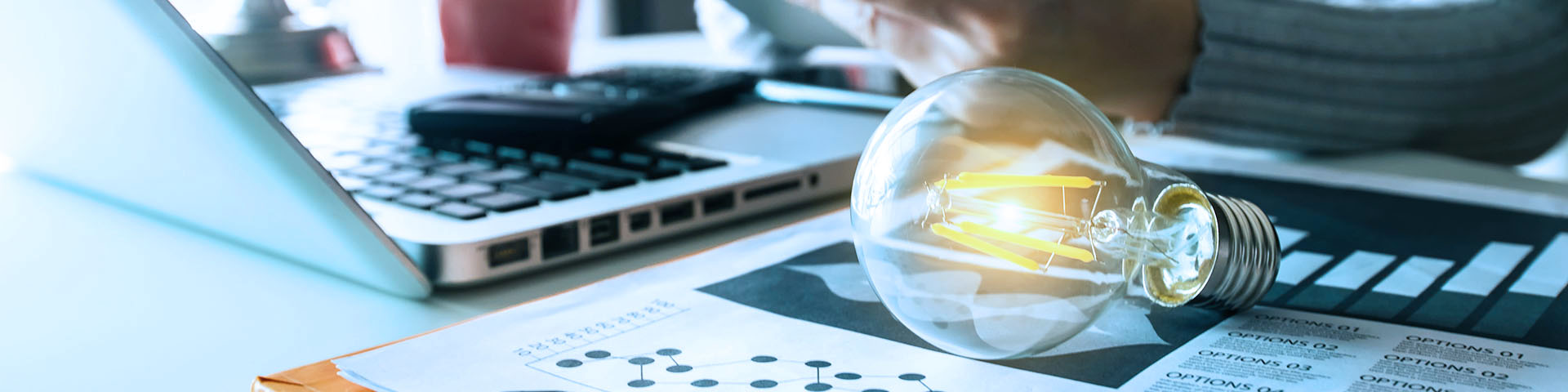
To achieve desired results, a continuous improvement methodology may be employed. This type of methodology is a series of iterative steps over many design generations. It is also known to be Lean Six Sigma. This article will present a variation of the PDSA methodology based on SIPOC analyses. Its application will be discussed in the context an engineering design studio.
Lean Six Sigma
Lean Six Sigma refers to a continuous improvement methodology that focuses on simplifying and making processes more predictable. Processes that are simpler result in fewer mistakes, which lowers the chance of them going wrong. The statistical process control (SPC), techniques are used to control process variables. This improves performance. This method can be used for improving any product or process. The company must set measurable parameters and use data as a guide to make changes.
PDSA
The PDSA continuous-improvement methodology is a loop of process design and analysis that then leads to action to improve a process. The study step of PDSA is the first phase. This evaluates the effectiveness of an experimental improvement compared to the planned results. This step also helps the team determine whether the improvement has been a measurable success or not. This step will allow the team to conduct analysis. They may use control charts to distinguish expected from special cause variation.
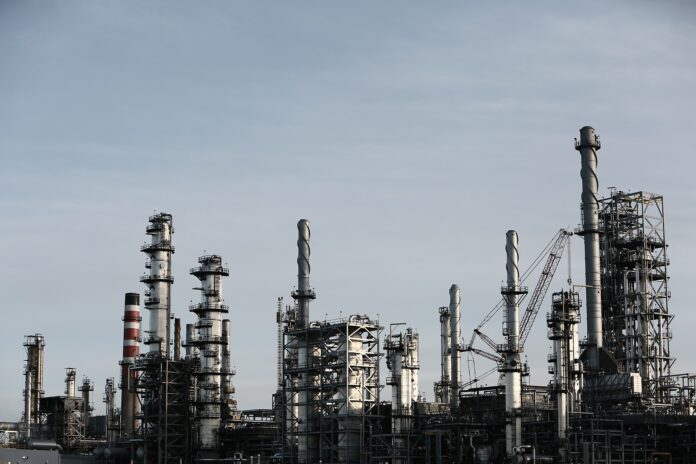
Variation of PDSA
PDSA is a process for continuous improvement and problem solving. It has a clear focus and measurable goals. The process starts with a careful planning stage, and then moves on to effective action. Every idea is then evaluated for sustainability and feasibility. The project team monitors the results and ensures that any improvement will be sustainable.
PDSA based upon SIPOC analysis
SIPOC analysis is a useful tool for improving business processes. It provides a simple way to categorize data in five categories. SIPOC diagrams can help teams better understand their processes by providing a high-level overview of each. They are also a great way to focus discussions.
PDSA based on DMAIC
Businesses looking to improve the efficiency of their processes will benefit from continuous improvement techniques that follow DMAIC. These methods are structured and straightforward, and they are designed to help organizations understand and eliminate ineffective processes while achieving measurable and sustainable results. Without the use of these tools, organizations may struggle to track which changes have the greatest impact and which ones don't. It can be difficult for them to implement effective controls.
PDSA based kanban board
Kanban boards have many advantages. You can visualize the work in progress and assign tasks to team members. Attachments or images can also be added to each task. They allow you to manage how much work you have completed and when it is complete.
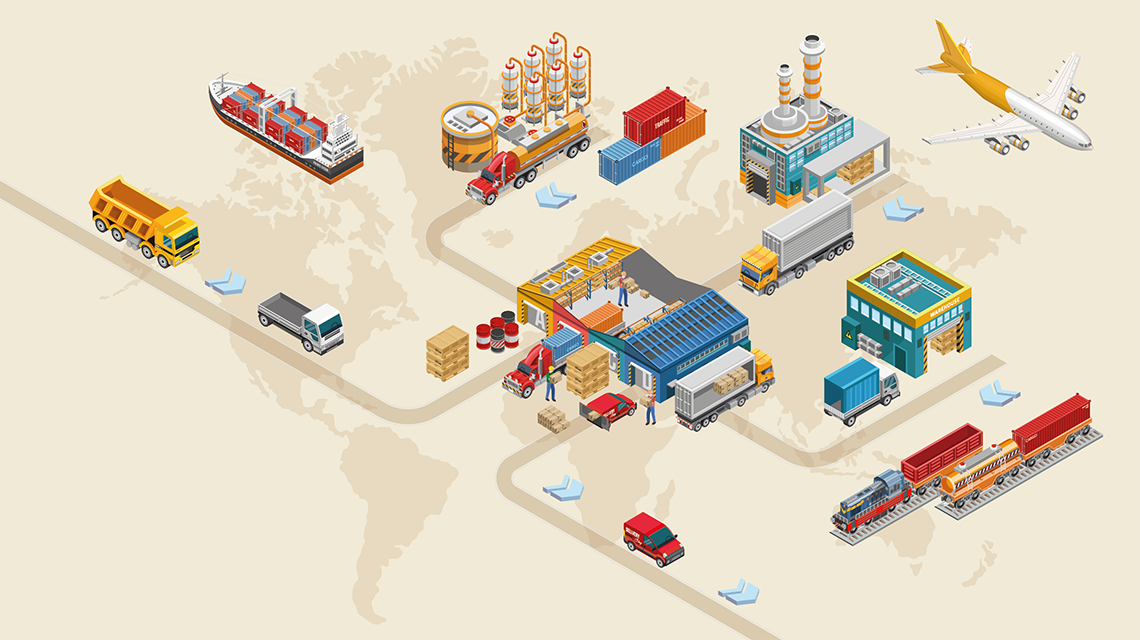
Kaizen based on SIPOC analysis
The SIPOC framework is an effective concept that can be used to improve process efficiency. It helps define the boundaries of a process, gather relevant information and present it in a clear and easily understandable manner. It is used in the Define phase to help identify process variations that may affect KVIPs (key performance indicators), and is especially useful. It also helps teams and other stakeholders plan improvements to improve a process.
PDSA based PDSA variations
PDSA (continuous improvement methodology) is based upon the principle of continuous comparability of actual and predicted results. The PDSA process measures actual and expected results from an improvement experiment. Then, the reality of the implementation of the plan is compared. The team then analyzes data to determine whether or not the experiment brought about measurable changes. This data is often categorized using a control chart, to help distinguish between expected variation and special cause variation.
FAQ
What is Six Sigma?
It's a strategy for quality improvement that emphasizes customer care and continuous learning. It is a method that eliminates defects using statistical techniques.
Motorola created Six Sigma as part of their efforts to improve manufacturing processes in 1986.
The idea spread quickly throughout the industry, and today, many organizations are using six sigma methods to improve product design, production, delivery, and customer service.
What are the steps in the decision-making process in management?
Managers are faced with complex and multifaceted decisions. It involves many elements, including analysis, strategy. planning. implementation. measurement. evaluation. feedback.
When managing people, the most important thing to remember is that they are just human beings like you and make mistakes. As such, there are always opportunities for improvement, especially when you put in the effort to improve yourself.
This video explains the process of decision-making in Management. We discuss different types of decisions as well as why they are important and how managers can navigate them. The following topics will be covered.
It seems so difficult sometimes to make sound business decisions.
Businesses are complex systems, and they have many moving parts. The people who run them must juggle multiple priorities at once while also dealing with uncertainty and complexity.
It is important to understand the effects of these factors on the system in order to make informed decisions.
It is important to consider the functions and reasons for each part of the system. Then, you need to think about how these pieces interact with one another.
It is also worth asking yourself if you have any unspoken assumptions about how you have been doing things. If you don't have any, it may be time to revisit them.
For help, ask someone else if you're still stumped after all the above. You may be able to see things from a different perspective than you are and gain insight that can help you find a solution.
How do we create a company culture that is productive?
A successful company culture is one that makes people feel valued and respected.
It is founded on three basic principles:
-
Everybody can contribute something valuable
-
People are treated with respect
-
People and groups should respect each other.
These values are reflected in the way people behave. They will treat others with kindness and consideration.
They will respect the opinions of others.
And they will encourage others to share ideas and feelings.
The company culture promotes collaboration and open communication.
People feel comfortable expressing their opinions freely without fear of reprisal.
They are aware that mistakes can be accepted if they are treated honestly.
The company culture promotes honesty, integrity, and fairness.
Everyone is aware that truth must be told.
Everyone recognizes that rules and regulations are important to follow.
People don't expect special treatment or favors.
What are the 3 basic management styles?
The three basic management styles are: authoritarian, laissez-faire, and participative. Each style has its advantages and disadvantages. Which style do YOU prefer? Why?
Authoritarian - The leader sets the direction and expects everyone to comply with it. This style is best when the organization has a large and stable workforce.
Laissez-faire is a leader who allows everyone to make their own decisions. This approach works best in small, dynamic organizations.
Participative – Leaders are open to suggestions and ideas from everyone. This style works best in smaller organizations where everyone feels valued.
What is the difference between Six Sigma Six Sigma and TQM?
The main difference between these two quality management tools is that six sigma focuses on eliminating defects while total quality management (TQM) focuses on improving processes and reducing costs.
Six Sigma can be described as a strategy for continuous improvement. It emphasizes the elimination of defects by using statistical methods such as control charts, p-charts, and Pareto analysis.
The goal of this method is to reduce variation in product output. This is done by identifying root causes and rectifying them.
Total Quality Management involves monitoring and measuring every aspect of the organization. It also involves training employees to improve performance.
It is frequently used as an approach to increasing productivity.
Statistics
- UpCounsel accepts only the top 5 percent of lawyers on its site. (upcounsel.com)
- Hire the top business lawyers and save up to 60% on legal fees (upcounsel.com)
- The BLS says that financial services jobs like banking are expected to grow 4% by 2030, about as fast as the national average. (wgu.edu)
- 100% of the courses are offered online, and no campus visits are required — a big time-saver for you. (online.uc.edu)
- The average salary for financial advisors in 2021 is around $60,000 per year, with the top 10% of the profession making more than $111,000 per year. (wgu.edu)
External Links
How To
What is Lean Manufacturing?
Lean Manufacturing uses structured methods to reduce waste, increase efficiency and reduce waste. They were created in Japan by Toyota Motor Corporation during the 1980s. The main goal was to produce products at lower costs while maintaining quality. Lean manufacturing seeks to eliminate unnecessary steps and activities in the production process. It is made up of five elements: continuous improvement, continuous improvement, just in-time, continuous change, and 5S. The production of only what the customer needs without extra work is called pull systems. Continuous improvement involves constantly improving upon existing processes. Just-intime refers the time components and materials arrive at the exact place where they are needed. Kaizen refers to continuous improvement. It is achieved through small changes that are made continuously. Five-S stands for sort. It is also the acronym for shine, standardize (standardize), and sustain. These five elements can be combined to achieve the best possible results.
Lean Production System
Six key concepts form the foundation of the lean production system:
-
Flow - focuses on moving information and materials as close to customers as possible.
-
Value stream mapping: This is a way to break down each stage into separate tasks and create a flowchart for the entire process.
-
Five S's – Sort, Put In Order Shine, Standardize and Sustain
-
Kanban - use visual signals such as colored tape, stickers, or other visual cues to keep track of inventory;
-
Theory of constraints: identify bottlenecks in your process and eliminate them using lean tools, such as kanban board.
-
Just-in-time delivery - Deliver components and materials right to your point of use.
-
Continuous improvement is making incremental improvements to your process, rather than trying to overhaul it all at once.