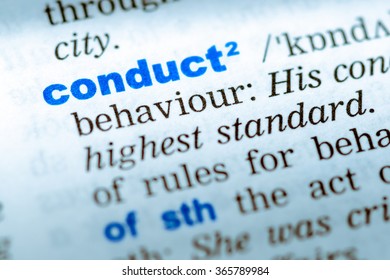
Last mile logistics are becoming more complicated as consumers are increasingly dependent on online channels to meet their needs. This article discusses the benefits and challenges of last-mile delivery, as well the costs. You'll find out how to improve your last mile delivery while maintaining operational excellence. Furthermore, you'll be able to learn more about new technologies that you can use to your advantage.
Last mile logistics challenges
Last mile logistics can be difficult for rural areas. Transport congestion and distances between urban and rural delivery points can make it difficult to deliver. With the increase in e-commerce, faster deliveries and free shipping have become more important than ever. This means that logistics companies need to improve delivery and fulfillment to meet customer demands.
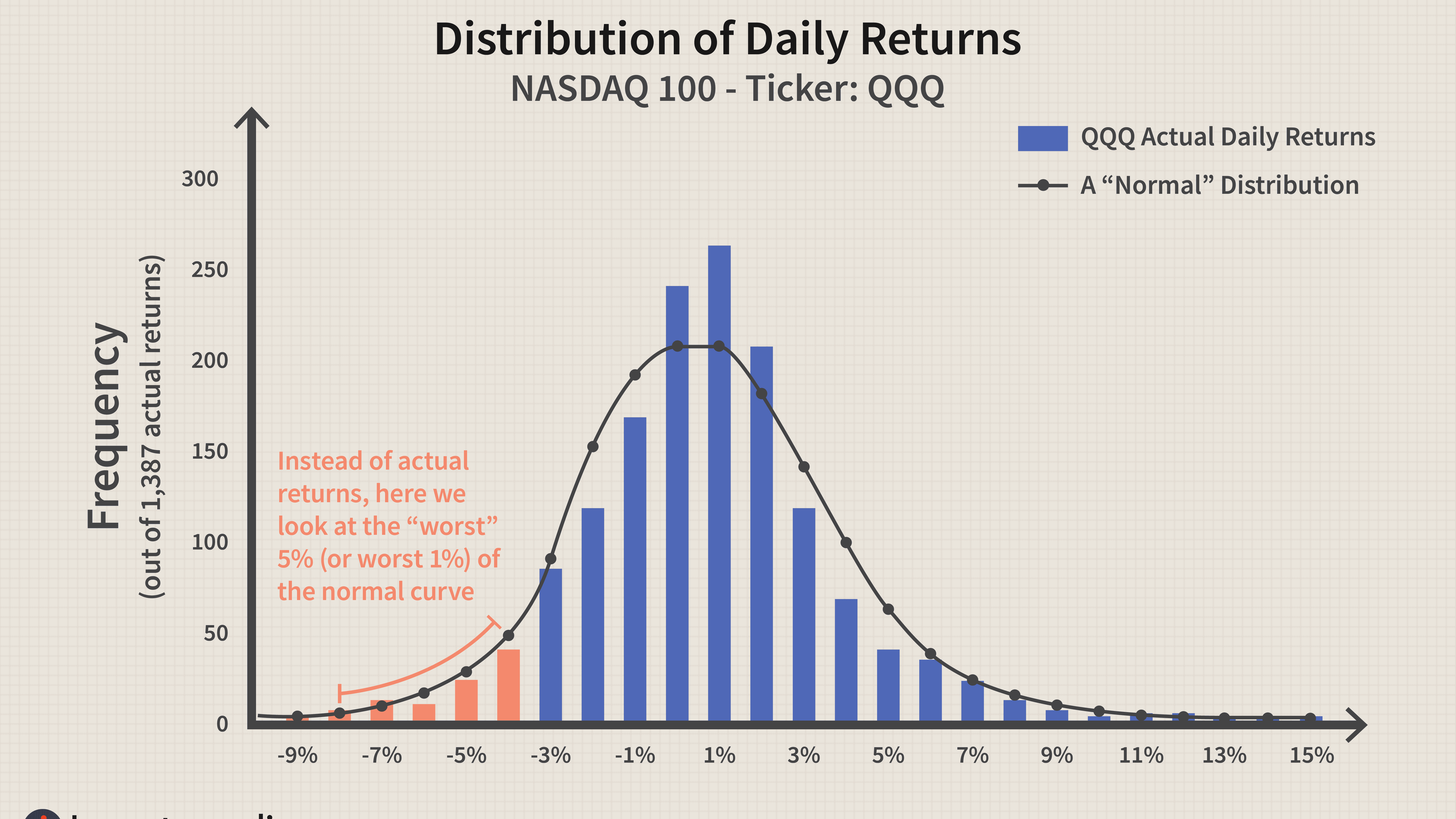
It is highly unpredictable that the last mile distribution process can be delayed, which can cause long journeys and insufficient transportation. These factors can increase costs and time lags, and companies must create contingency plans for unexpected incidents. For example, if one driver is sick and unable to deliver the product on time, operators must quickly dispatch a replacement driver.
While last mile logistics is challenging, new technologies can make delivery faster and more efficient. Route optimization technology, for example, is able detect the most cost efficient routes. This will help to save both time AND money. Advanced machine-learning systems analyze road conditions, weather patterns, and traffic congestion to determine the best route. Advanced software can help drivers plan their routes and avoid collisions.
Benefits of third-party logistics providers
Businesses have a variety of benefits from third-party logistics companies. They can expand to new markets, scale inventory to meet demand and reduce overhead when demand falls. This helps businesses reach new markets and improve service. They can also benefit from a much more reliable and consistent supply chain, which is often less expensive than managing their own logistics.
Outsourcing logistics is a great alternative because it allows the company to focus on its core business. It reduces stress associated with handling non-core logistical tasks. Third-party logistics companies can also design custom shipping labels for special orders. Of course, these services come with a cost, so be sure to plan ahead and prepare a shipping insurance policy. This insurance will cover you for any shipping mishaps.
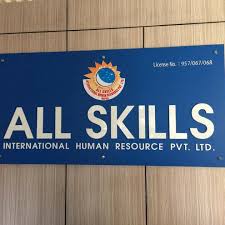
Third-party logistic providers are also available to help eCommerce businesses with warehouse space and inventory management. These providers can also deliver goods quickly to customers, which is a huge benefit for eCommerce companies that are growing. Third-party logistics providers will manage stock management and replenish stock as necessary. They can also update inventory in the event that a customer returns an item.
FAQ
Why does it sometimes seem so hard to make good business decisions
Businesses are complex systems, and they have many moving parts. People who manage them have to balance multiple priorities while dealing with complexity and uncertainty.
Understanding the impact of these factors on the system is crucial to making sound decisions.
To do this, you must think carefully about what each part of the system does and why. Next, consider how each piece interacts with the others.
Also, you should ask yourself if there have been any assumptions in your past behavior. If so, it might be worth reexamining them.
For help, ask someone else if you're still stumped after all the above. They may see things differently from you and have insights that could help you find a solution.
What is the difference in Six Sigma and TQM?
The key difference between the two quality management tools is that while six-sigma focuses its efforts on eliminating defects, total quality management (TQM), focuses more on improving processes and reducing cost.
Six Sigma can be described as a strategy for continuous improvement. It emphasizes the elimination of defects by using statistical methods such as control charts, p-charts, and Pareto analysis.
This method attempts to reduce variations in product output. This is accomplished by identifying the root cause of problems and fixing them.
Total Quality Management involves monitoring and measuring every aspect of the organization. This includes training employees to improve their performance.
It is frequently used as an approach to increasing productivity.
What is the difference in leadership and management?
Leadership is about influence. Management is about controlling others.
A leader inspires others while a manager directs them.
A leader inspires others to succeed, while a manager helps workers stay on task.
A leader develops people; a manager manages people.
Six Sigma is so popular.
Six Sigma is easy to implement and can produce significant results. It also provides a framework for measuring improvements and helps companies focus on what matters most.
How does a manager motivate his/her employees?
Motivation refers to the desire to perform well.
You can get motivated by doing something enjoyable.
You can also get motivated by seeing your contribution to the success or the improvement of the organization.
You might find it more rewarding to treat patients than to study medical books if you plan to become a doctor.
The inner motivation is another type.
You may feel strongly that you are responsible to help others.
You may even find it enjoyable to work hard.
Ask yourself why you aren't feeling motivated.
Then, consider ways you could improve your motivation.
Statistics
- Hire the top business lawyers and save up to 60% on legal fees (upcounsel.com)
- Your choice in Step 5 may very likely be the same or similar to the alternative you placed at the top of your list at the end of Step 4. (umassd.edu)
- This field is expected to grow about 7% by 2028, a bit faster than the national average for job growth. (wgu.edu)
- The profession is expected to grow 7% by 2028, a bit faster than the national average. (wgu.edu)
- 100% of the courses are offered online, and no campus visits are required — a big time-saver for you. (online.uc.edu)
External Links
How To
How can you implement the Kaizen technique?
Kaizen means continuous improvement. The term was coined in the 1950s at Toyota Motor Corporation and refers to the Japanese philosophy emphasizing constant improvement through small incremental changes. It's where people work together in order to improve their processes constantly.
Kaizen is one of Lean Manufacturing's most efficient methods. In this concept, employees who are responsible for the production line must identify problems that exist during the manufacturing process and try to solve them before they become big issues. This will increase the quality and decrease the cost of the products.
Kaizen is an approach to making every worker aware and alert to what is happening around them. If something is wrong, it should be corrected immediately so that no problem occurs. So, if someone notices a problem while working, he/she should report it to his/her manager.
When doing kaizen, there are some principles we must follow. Start with the end product, and then move to the beginning. To improve our factory, for example, we need to fix the machines that produce the final product. We then fix the machines producing components, and the machines producing raw materials. We then fix the workers that work with those machines.
This is why it's called "kaizen" because it works step-by-step to improve everything. Once the factory is fixed, we return to the original site and work our way back until we get there.
How to measure kaizen's effectiveness in your business is essential to implement it. There are many ways to tell if kaizen is effective. Another way to determine if kaizen is working well is to look at the quality of the products. Another way is to check how much productivity has grown since kaizen was implemented.
To determine if kaizen is effective, you should ask yourself why you chose to implement kaizen. Was it just because it was the law or because you wanted to save money? Did you really believe that it would be a success factor?
Suppose you answered yes to any of these questions, congratulations! You're ready to start kaizen.