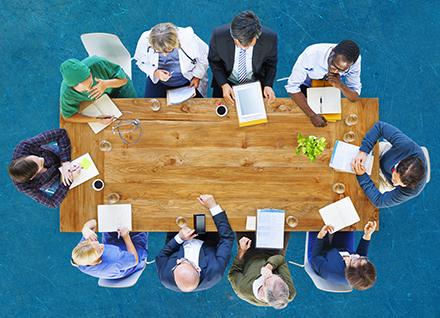
The negative impact of change fatigue on employee engagement and productivity is an important issue that must be addressed in organizations. One of the most serious effects of change fatigue is employee turnover. This article examines the causes and effects of workplace change fatigue. It also contains some ways to combat change fatigue. You can read on for more. This article examines three areas that are important in change fatigue: organizational change fatigue; employee engagement and turnover; and the need to change organizational culture.
Impact of change fatigue on employee productivity
Change fatigue is not a new phenomenon. It can have a significant impact on employee productivity. Employees are charged with adjusting to new technologies and ways of working, and they do not always have the power to decide whether they like the changes. Therefore, employees should be involved in the decision-making process of businesses. Before implementing new technology, or solutions, businesses can get employee feedback. This will help you to identify any concerns or questions about the solution. These concerns can be identified and addressed by a proactive approach to employee mental well-being.
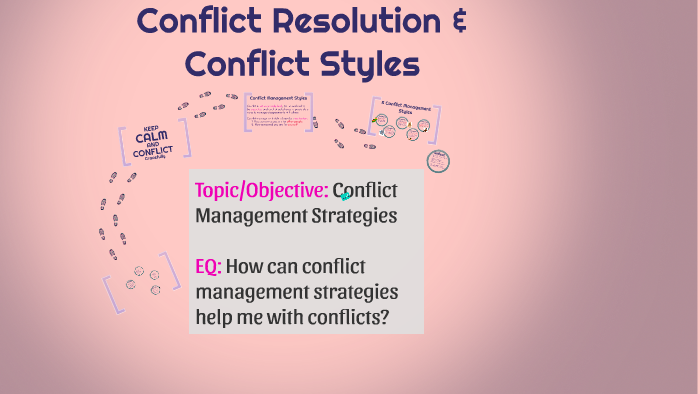
Gartner research found that smaller changes cause greater fatigue than larger, structural changes. This means that changes affecting day-to-day life will affect employees 2.5 times more than larger structural changes. This is bad news for organizations, but it doesn't have to be that way. They can significantly reduce the chance of change fatigue if managers are proactive about how change will impact their organization and create an environment for change.
Employee engagement is affected by change fatigue
When organizations undergo significant changes, one of the most important factors to consider is the impact of change fatigue. Gartner found that employees are 2.5x as likely to be tired of change when changes are smaller. There are many ways to reduce change fatigue. Identifying the causes of fatigue and reducing them early on can help you avoid the problem. Here are some tips to help your employees stay engaged and productive during major transitions.
Change fatigue is caused by the introduction or modification of systems and processes. As a result, many people become disengaged with the change process. One survey found that nearly 75% of people aged 16-24 and 66% over 65 suffer from change fatigue. Change fatigue is more common in women than in men. This number is even greater for small and medium-sized employees. Change fatigue can also have a negative effect on a company’s bottom line. It will cause employees to be less motivated, and less engaged with the new system.
Impact of change fatigue on employee turnover
Whether you're a small business or a large corporation, the economy can have a significant impact on the health of your company. Companies may need to make drastic changes to their services or cut staff during economic uncertainty. This can cause employees to become "change-fatigued", which can have a negative impact on their productivity. There are options to minimize the effects change fatigue. Andreatta's graph provides an excellent starting point.
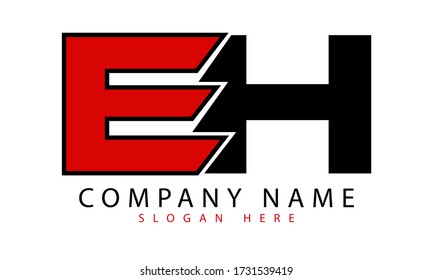
Business leaders are increasingly concerned about the impact of change fatigue on employee motivation. Businesses leaders must be aware that employees who have experienced months of rapid organizational or business change could feel more overwhelmed than they can handle. This could cause a drop in employee engagement and decrease in turnover. The consequences of change fatigue can adversely impact your business, whether you're small or large. Change fatigue can be a sign of a larger problem. It should be treated seriously.
FAQ
What are the steps that management takes to reach a decision?
Managers are faced with complex and multifaceted decisions. It involves many factors, such as analysis and strategy, planning, execution, measurement, evaluation, feedback etc.
It is important to remember that people are human beings, just like you. They make mistakes. As such, there are always opportunities for improvement, especially when you put in the effort to improve yourself.
In this video, we explain what the decision-making process looks like in Management. We discuss different types of decisions as well as why they are important and how managers can navigate them. Here are some topics you'll be learning about:
How does a manager develop his/her management skills?
It is important to have good management skills.
Managers must constantly monitor the performance of their subordinates.
It is important to take immediate action if your subordinate doesn't perform as expected.
It is important to be able identify areas that need improvement and what can be done to improve them.
What are management concepts, you ask?
Management concepts are the fundamental principles and practices that managers use when managing people and their resources. They cover topics like job descriptions (job descriptions), performance evaluations, training programmes, employee motivation and compensation systems.
Statistics
- As of 2020, personal bankers or tellers make an average of $32,620 per year, according to the BLS. (wgu.edu)
- This field is expected to grow about 7% by 2028, a bit faster than the national average for job growth. (wgu.edu)
- UpCounsel accepts only the top 5 percent of lawyers on its site. (upcounsel.com)
- The profession is expected to grow 7% by 2028, a bit faster than the national average. (wgu.edu)
- 100% of the courses are offered online, and no campus visits are required — a big time-saver for you. (online.uc.edu)
External Links
How To
How can Lean Manufacturing be done?
Lean Manufacturing is a method to reduce waste and increase efficiency using structured methods. They were created by Toyota Motor Corporation in Japan in the 1980s. The primary goal was to make products with lower costs and maintain high quality. Lean manufacturing focuses on eliminating unnecessary steps and activities from the production process. It consists of five basic elements: pull systems, continuous improvement, just-in-time, kaizen (continuous change), and 5S. Pull systems are able to produce exactly what the customer requires without extra work. Continuous improvement means continuously improving on existing processes. Just-intime refers the time components and materials arrive at the exact place where they are needed. Kaizen is continuous improvement. This can be achieved by making small, incremental changes every day. Five-S stands for sort. It is also the acronym for shine, standardize (standardize), and sustain. These five elements work together to produce the best results.
Lean Production System
The lean production system is based on six key concepts:
-
Flow - focuses on moving information and materials as close to customers as possible.
-
Value stream mapping- This allows you to break down each step of a process and create a flowchart detailing the entire process.
-
Five S's: Sort, Shine Standardize, Sustain, Set In Order, Shine and Shine
-
Kanban - use visual signals such as colored tape, stickers, or other visual cues to keep track of inventory;
-
Theory of constraints: identify bottlenecks in your process and eliminate them using lean tools, such as kanban board.
-
Just-intime - Order components and materials at your location right on the spot.
-
Continuous improvement: Make incremental improvements to the process instead of overhauling it completely.