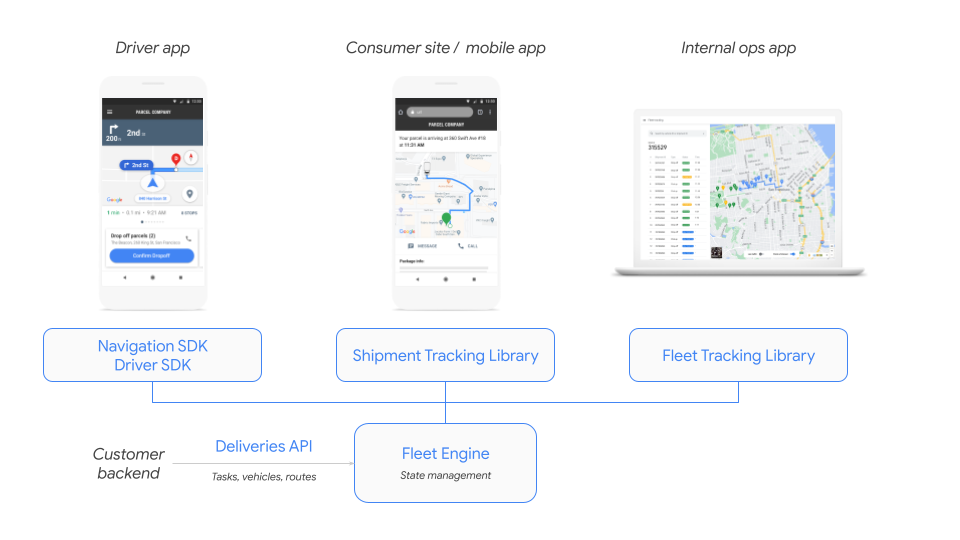
There are four fundamental management perspectives. These perspectives are Theory. Function. Historical Development. and Future Trends. This article discusses each perspective. Each perspective has both its benefits and drawbacks. It is important to know the differences between each viewpoint. Then you will be able to choose the one which best suits your needs. Here are some examples.
Theories of management
Theories of management are important in determining the appropriate management strategy for an organization. Different theories of management focus on different aspects. However, they all relate to management. Although no one theory is right for every organization, it's possible to combine different theories to produce better results. In fact, many modern organizations employ a mixture of theories, leading to more flexible organizational structures.
Theories of management are used in different settings, from management in general to project management. In the project management context, they can be viewed as condensed pieces of knowledge that enable novices to do what an expert would do. They are most effective when used in small projects where theoretical issues can be resolved without having to pay more. However, in large projects, they can seriously damage performance and lead to problems that could have been avoided with better management practices.
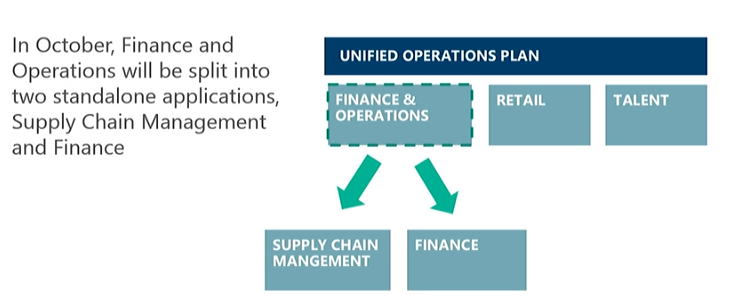
Functions of management
For an organisation to succeed, its management functions are essential. These include planning, identifying the tasks, monitoring and correcting any problems. An organization's management plays an important role, especially in achieving its goals regarding profit and market share. Managers have to make decisions and implement strategies.
Planning is the first stage of the management process. This involves setting goals and defining the purpose. This requires the ability and skills to analyse and comprehend past and present trends and develop and implement future strategic plans. An organisation can achieve its objectives if it performs these functions well.
Historical development
Management has evolved over the years with new theories that emphasize the human factor. Douglas McGregor's Theory Y, which is a well-known example of this change, is a great example. It changed the traditional notion of executive roles, changing the perception of them as managers to being coaches. The emphasis on emotional intelligence and human management was changed by organizational theorists.
The Industrial Revolution was the catalyst for intense debate regarding management theory. This was a pivotal moment in the history management. The ensuing changes led to the emergence of six main management theories. Each theory addresses different aspects management.
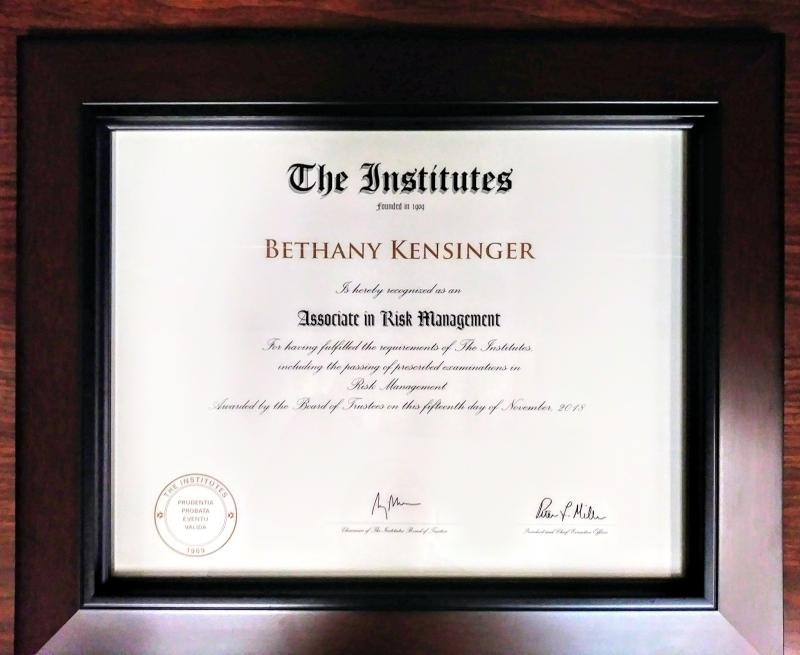
Future trends
Trends that influence the workplace environment are shaping the future direction of management. One of these trends concerns the changing role that managers play. This requires managers to be more flexible and agile. Flexibility working is becoming more popular in the UK. Over half of managers believe flexible working will be the norm within five to ten years. Half also think their direct reports are more flexible than five years ago.
The importance of building working relationships is one trend that is impacting the management sector. More than half of managers recognise this as a future trend and believe that they are more important now than five years ago. Flexibility is a contributing factor to this trend. Due to the economic crisis, some people have had to pay more attention and build trust with their friends. These new trends can help companies attract, develop and retain employees.
FAQ
What is Six Sigma?
It is a way to improve quality that places emphasis on customer service and continuous learning. This is an approach to quality improvement that uses statistical techniques to eliminate defects.
Motorola's 1986 efforts to improve manufacturing process efficiency led to the creation of Six Sigma.
The idea spread quickly in the industry. Today many organizations use six-sigma techniques to improve product design.
Why does it sometimes seem so hard to make good business decisions
Complex systems with many moving parts are the hallmark of businesses. Their leaders must manage multiple priorities, as well as dealing with uncertainty.
Understanding how these factors impact the whole system is key to making informed decisions.
To do this, you must think carefully about what each part of the system does and why. It is important to then consider how the individual pieces relate to each other.
Ask yourself if there are hidden assumptions that have influenced your behavior. If they don't, you may want to reconsider them.
For help, ask someone else if you're still stumped after all the above. They might see things differently than you and may have some insights that could help find a solution.
Six Sigma is so well-known.
Six Sigma is simple to implement and can yield significant results. It provides a framework that allows for improvement and helps companies concentrate on what really matters.
What is TQM and how can it help you?
When manufacturing companies realized that price was not enough to compete, the industrial revolution brought about the quality movement. If they wanted to stay competitive, they needed to improve their quality and efficiency.
To address this need for improvement management created Total Quality Management (TQM) which aimed to improve all aspects of an organization's performance. It included continuous improvement, employee involvement and customer satisfaction.
What is Kaizen, exactly?
Kaizen is a Japanese term which means "continuous improvement." This philosophy encourages employees to continually look for ways to improve the work environment.
Kaizen is a belief that everyone should have the ability to do their job well.
What is the role of a manager in a company?
The role of a manager varies from one industry to another.
A manager is generally responsible for overseeing the day to day operations of a company.
He/she ensures the company meets its financial commitments and produces goods/services that customers demand.
He/she is responsible for ensuring that employees comply with all regulations and follow quality standards.
He/she plans new products and services and oversees marketing campaigns.
How does a manager motivate his/her employees?
Motivation refers to the desire or need to succeed.
Enjoyable activities can motivate you.
You can also feel motivated by making a positive contribution to the success in the organization.
If you are a doctor and want to be one, it will likely be more rewarding to see patients than to read medical books every day.
A different type of motivation comes directly from the inside.
Perhaps you have a strong sense to give back, for example.
Perhaps you enjoy working hard.
Ask yourself why you feel so motivated.
Then think about how you can make your life more motivating.
Statistics
- UpCounsel accepts only the top 5 percent of lawyers on its site. (upcounsel.com)
- The profession is expected to grow 7% by 2028, a bit faster than the national average. (wgu.edu)
- As of 2020, personal bankers or tellers make an average of $32,620 per year, according to the BLS. (wgu.edu)
- The average salary for financial advisors in 2021 is around $60,000 per year, with the top 10% of the profession making more than $111,000 per year. (wgu.edu)
- Hire the top business lawyers and save up to 60% on legal fees (upcounsel.com)
External Links
How To
How does Lean Manufacturing work?
Lean Manufacturing is a method to reduce waste and increase efficiency using structured methods. These processes were created by Toyota Motor Corporation, Japan in the 1980s. It was designed to produce high-quality products at lower prices while maintaining their quality. Lean manufacturing eliminates unnecessary steps and activities from a production process. It is made up of five elements: continuous improvement, continuous improvement, just in-time, continuous change, and 5S. Pull systems involve producing only what the customer wants without any extra work. Continuous improvement is constantly improving upon existing processes. Just-intime refers the time components and materials arrive at the exact place where they are needed. Kaizen means continuous improvement, which is achieved by implementing small changes continuously. Finally, 5S stands for sort, set in order, shine, standardize, and sustain. These five elements can be combined to achieve the best possible results.
Lean Production System
Six key concepts underlie the lean production system.
-
Flow - focuses on moving information and materials as close to customers as possible.
-
Value stream mapping is the ability to divide a process into smaller tasks, and then create a flowchart that shows the entire process.
-
Five S's, Sort, Set in Order, Shine. Standardize. and Sustain.
-
Kanban – visual signals like colored tape, stickers or other visual cues are used to keep track inventory.
-
Theory of Constraints - Identify bottlenecks in the process, and eliminate them using lean tools such kanban boards.
-
Just-in-time - deliver components and materials directly to the point of use;
-
Continuous improvement - make incremental improvements to the process rather than overhauling it all at once.