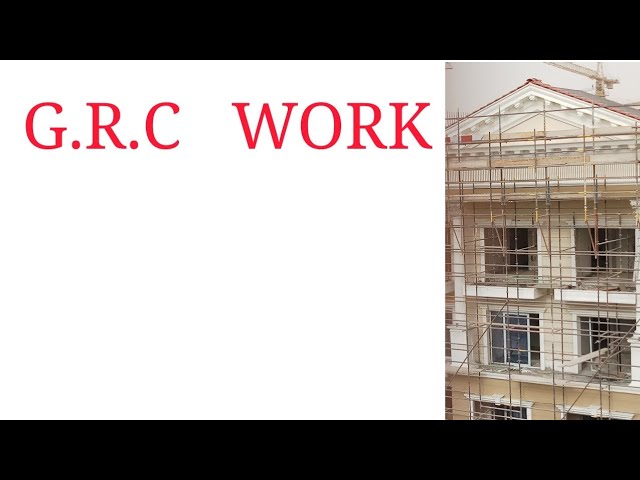
Risk Management refers to a way of reducing the chance of loss or harm within an organization. This involves planning for potential negative outcomes and reducing the risk of profit-chasing and escalation. This process is critical to the success of any business. The benefits of risk management are numerous. Here are some:
This decreases the probability of adverse events
Effective risk management begins with establishing a clear goal and a system to evaluate and reduce risks. Because it is counter to many of our biases as humans, risk management can be difficult. However, rules and compliance are effective in reducing some risks. Management must be proactive. That means managers must think through risks strategically, implement processes to address them and monitor and manage risks accordingly.
Reduces the likelihood of escalation
The best way to reduce risk of escalation is to create game plans that address all possible situations. Although most risks don't have an end point, having a plan can help your company be prepared for any eventuality. This will allow you to reduce the possibility of escalation as well as minimize any potential damage.
Reduces profit-chasing
There is a lot of talk these days about risk management. Risk management is taking the necessary steps to avoid potential loss. In order to avoid an increase in fuel costs, airlines might use financial derivatives. In order to protect their buildings from earthquakes, companies can raise their construction costs. In order to reduce their costs, companies may work with others that are facing similar risks.
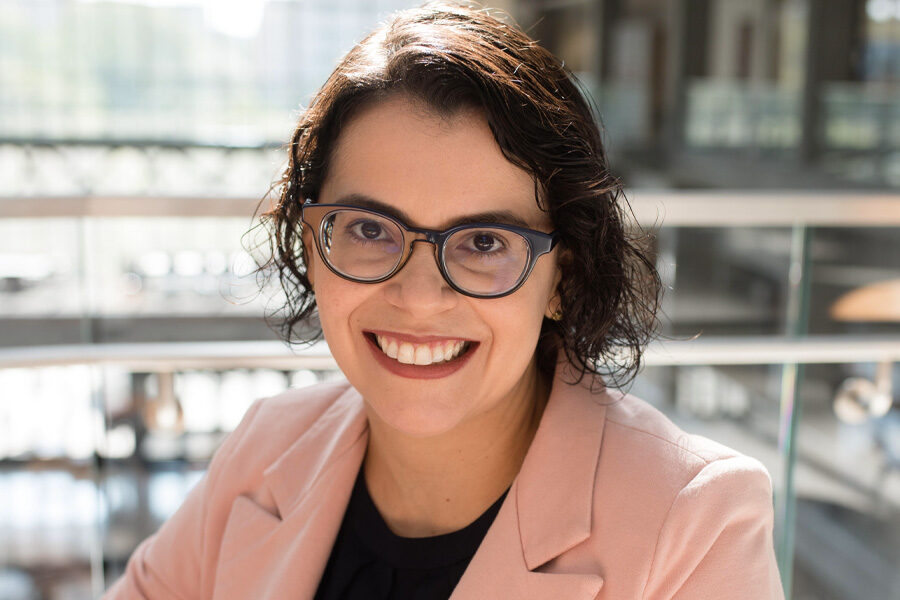
FAQ
It can sometimes seem difficult to make business decisions.
Complex systems and many moving parts make up businesses. Their leaders must manage multiple priorities, as well as dealing with uncertainty.
To make good decisions, you must understand how these factors affect the entire system.
You must first consider what each piece of the system does and why. It is important to then consider how the individual pieces relate to each other.
You need to ask yourself if your previous actions have led you to make unfounded assumptions. If not, you might want to revisit them.
You can always ask someone for help if you still have questions after all of this. They might see things differently than you and may have some insights that could help find a solution.
What is TQM and how can it help you?
The industrial revolution was when companies realized that they couldn't compete on price alone. This is what sparked the quality movement. If they wanted to stay competitive, they needed to improve their quality and efficiency.
Management developed Total Quality Management to address the need for improvement. It focused on all aspects of an organisation's performance. It included continuous improvement and employee involvement as well as customer satisfaction.
What are the main styles of management?
These are the three most common management styles: participative (authoritarian), laissez-faire (leavez-faire), and authoritarian. Each style has its advantages and disadvantages. What style do you prefer? Why?
Authority - The leader is the one who sets the direction and expects everyone in the organization to follow it. This style works well if an organization is large and stable.
Laissez-faire: The leader lets each person decide for themselves. This style is most effective when the organization's size and dynamics are small.
Participative – Leaders are open to suggestions and ideas from everyone. This style is best for small organizations where everyone feels valued.
What are some common mistakes managers make?
Managers can make their jobs more difficult than necessary.
They may not be able to delegate enough responsibility to staff or provide adequate support.
Managers often lack the communication skills necessary to motivate and guide their teams.
Some managers create unrealistic expectations for their teams.
Managers may attempt to solve all problems themselves, rather than delegating it to others.
How does a manager motivate his/her employees?
Motivation is the desire for success.
Doing something that is enjoyable can help you get motivated.
Another way to get motivated is to see yourself as a contributor to the success of the company.
You might find it more rewarding to treat patients than to study medical books if you plan to become a doctor.
The inner motivation is another type.
One example is a strong sense that you are responsible for helping others.
Or you might enjoy working hard.
If you don't feel motivated, ask yourself why.
You can then think of ways to improve your motivation.
Statistics
- 100% of the courses are offered online, and no campus visits are required — a big time-saver for you. (online.uc.edu)
- Hire the top business lawyers and save up to 60% on legal fees (upcounsel.com)
- Our program is 100% engineered for your success. (online.uc.edu)
- The profession is expected to grow 7% by 2028, a bit faster than the national average. (wgu.edu)
- UpCounsel accepts only the top 5 percent of lawyers on its site. (upcounsel.com)
External Links
How To
How can you implement the Kaizen technique?
Kaizen means continuous improvement. This term was first used by Toyota Motor Corporation in the 1950s. It refers to the Japanese philosophy that emphasizes continuous improvement through small incremental changes. It's a team effort to continuously improve processes.
Kaizen is one the most important methods of Lean Manufacturing. In this concept, employees who are responsible for the production line must identify problems that exist during the manufacturing process and try to solve them before they become big issues. This is how you can improve the quality and lower the cost.
The main idea behind kaizen is to make every worker aware of what happens around him/her. Correct any errors immediately to avoid future problems. It is important that employees report any problems they see while on the job to their managers.
Kaizen has a set of basic principles that we all follow. Always start with the end product in mind and work our way back to the beginning. To improve our factory, for example, we need to fix the machines that produce the final product. Next, we repair the machines that make components. Then, the machines that make raw materials. And finally, we fix the workers who work directly with those machines.
This method is known as kaizen because it focuses upon improving every aspect of the process step by step. After we're done with the factory, it's time to go back and fix the problem.
You need to know how to measure the effectiveness of kaizen within your business. There are many methods to assess if kaizen works well. One method is to inspect the finished products for defects. Another way is determining how much productivity increased after implementing kaizen.
If you want to find out if your kaizen is actually working, ask yourself why. Was it just because it was the law or because you wanted to save money? It was a way to save money or help you succeed.
Suppose you answered yes to any of these questions, congratulations! You're now ready to get started with kaizen.