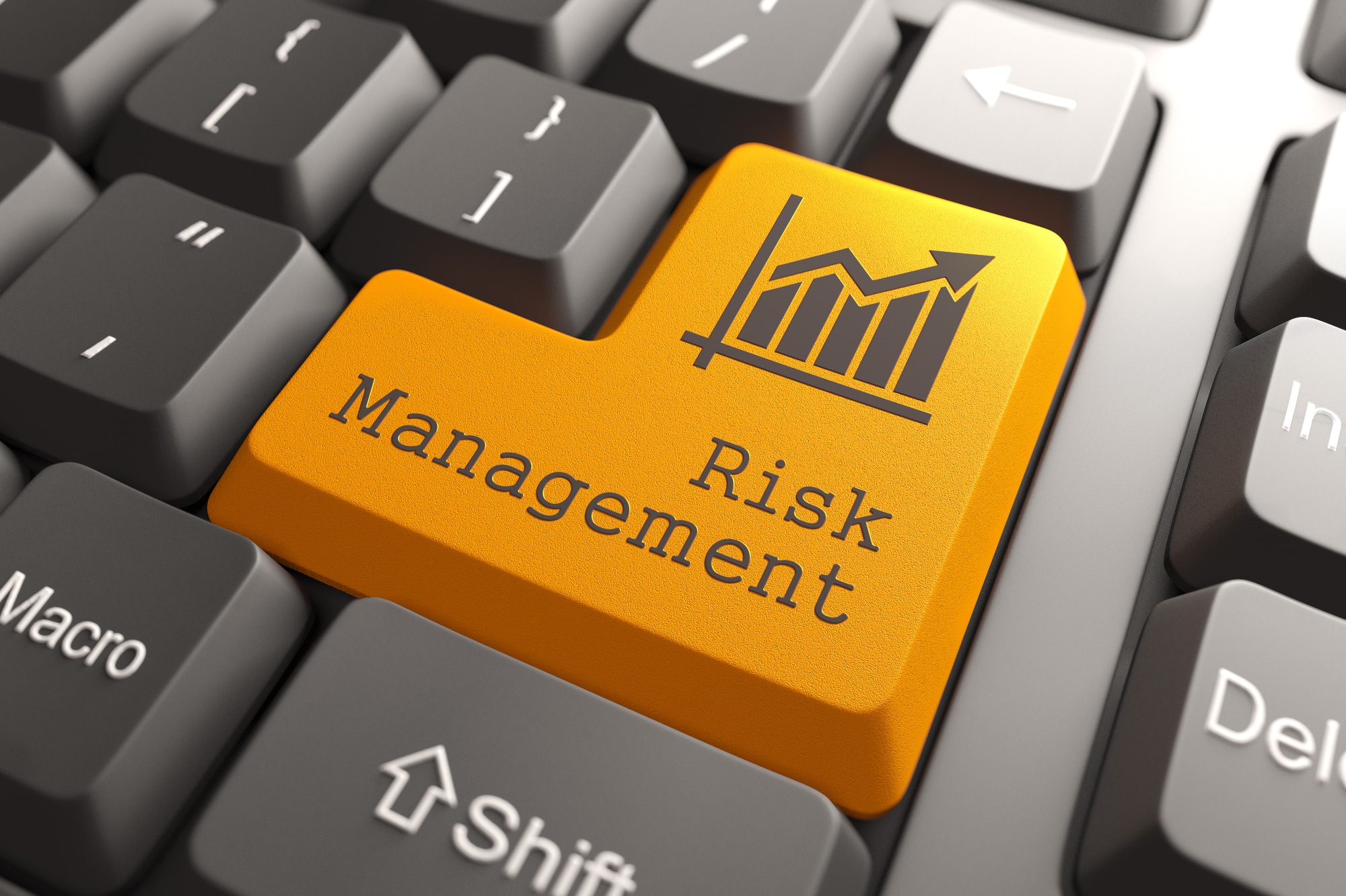
Process safety management is an organized approach to the management and integrity of all operating systems within a facility. This system must be up-to-date at least five years after it is established. The goal of process safety management (PSM) is to prevent any incidents. These steps will help you get started with process management. These steps will help ensure your facility is as safe as it can be and to prevent accidents.
Process safety management refers to a structured approach for managing the integrity operating systems and processes.
Process safety management's goal is to decrease the number of incidents. This will increase sustained value and productivity. It focuses on controlling risks within the plant and inherently safer equipment. It requires strict adherence to operating procedures, hazard assessment, and rigorous compliance with all regulations. It also includes training and maintenance of the plant, including effective and disciplined process control. It is an integral part of any safety-conscious organization.
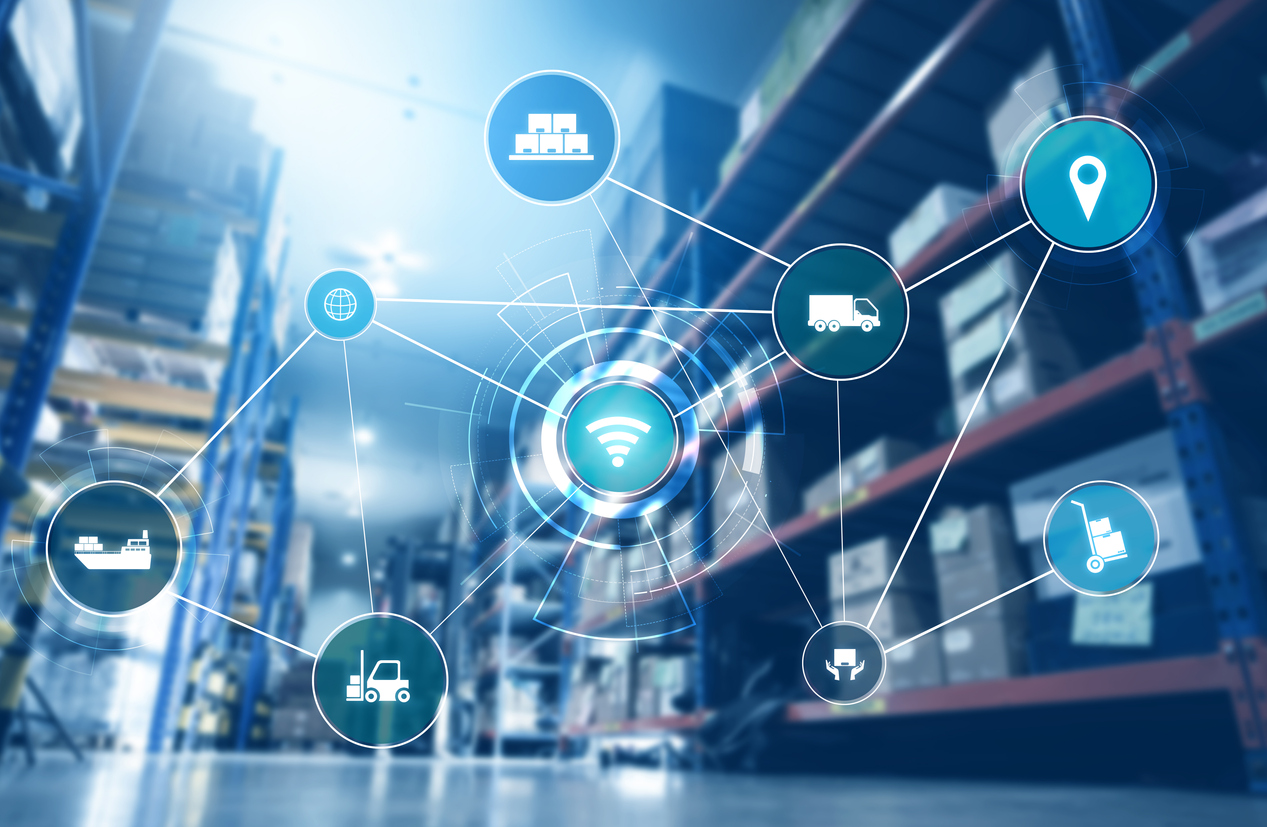
It must be kept current every 5 year
OSHA requires that the processes be reviewed and maintained regularly. This includes the development or updating of procedures and process safety information. All employees should have access to the information. Written investigation reports, procedures, and other documents must be kept for 5 years. Employees must have access to current process safety information that they can review and follow. To help employers meet their needs, they can turn to safety risk management experts.
It is required for major hazard areas
The legal requirement to implement a process safety control system for all major hazards is the process safety management program. Employers must not only develop and implement the plan, but also establish a procedure to ensure that employees are evacuated quickly and safely. This plan should include a safety alarm that alerts employees to evacuate. The plan should include emergency procedures for employees who are unable to evacuate from the hazardous area.
It helps prevent incidents
A well-designed process safety system can help improve profitability, safety performance, as well as quality. It can also improve a company's environmental responsibility. In addition, it helps reduce the risk of incidents. These are all vital areas to ensure the company's long-term success. Below is a short overview of the numerous benefits of a safety management system. In short, it helps a company prevent accidents and improve the health and safety of its employees and customers.
It takes a lot of time.
Process safety management can be complicated and time-consuming in a hazardous chemical plant. OSHA doesn't regulate the implementation of process safety management systems, but it does require facilities with at least 14 requirements to submit a written plan. Many companies use spreadsheets and forms to gather data and compile risk assessment and other information. This is tedious and can result in human error.
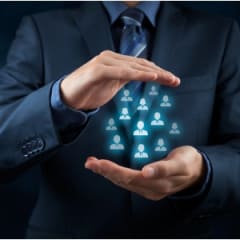
It involves employee participation
Pennsylvania State University adopted an employee participation element to its PSM program. This element draws upon employees' expertise, knowledge, as well as unique perspectives to enhance safety. This program details the different methods of employee participation and sets minimum requirements. It is crucial to involve all employees in process safety management and include them in all aspects. To avoid serious incidents, employee participation in PSM can be crucial. But, how do you ensure that all employees are engaged in the program?
FAQ
What does "project management" mean?
We mean managing the activities involved in carrying out a project.
These include planning the scope and identifying the needs, creating the budget, organizing the team, scheduling the work and monitoring progress. Finally, we close down the project.
How can a manager motivate his/her staff?
Motivation can be defined as the desire to achieve success.
Enjoyable activities can motivate you.
Or you can get motivated by seeing yourself making a contribution to the success of the organization.
For example, if you want to become a doctor, you'll probably find it more motivating to see patients than to study medicine books all day.
The inner motivation is another type.
You might feel a strong sense for responsibility and want to help others.
Perhaps you enjoy working hard.
Ask yourself why you aren't feeling motivated.
Then think about how you can make your life more motivating.
What are the four main functions of management?
Management is responsible for planning, organizing, directing, and controlling people and resources. This includes setting goals, developing policies and procedures, and creating procedures.
Management helps an organization achieve its objectives by providing direction, coordination, control, leadership, motivation, supervision, training, and evaluation.
These are the four major functions of management:
Planning - Planning refers to deciding what is needed.
Organizing: Organizing refers to deciding how things should work.
Directing - Directing means getting people to follow instructions.
Controlling: Controlling refers to making sure that people do what they are supposed to.
Six Sigma is so well-known.
Six Sigma can be implemented quickly and produce impressive results. It provides a framework that allows for improvement and helps companies concentrate on what really matters.
How can a manager enhance his/her leadership skills?
Good management skills are essential for success.
Managers must constantly monitor the performance of their subordinates.
You must quickly take action if your subordinate fails to perform.
You must be able to spot what is lacking and how you can improve it.
Statistics
- The BLS says that financial services jobs like banking are expected to grow 4% by 2030, about as fast as the national average. (wgu.edu)
- Hire the top business lawyers and save up to 60% on legal fees (upcounsel.com)
- UpCounsel accepts only the top 5 percent of lawyers on its site. (upcounsel.com)
- 100% of the courses are offered online, and no campus visits are required — a big time-saver for you. (online.uc.edu)
- The average salary for financial advisors in 2021 is around $60,000 per year, with the top 10% of the profession making more than $111,000 per year. (wgu.edu)
External Links
How To
How is Lean Manufacturing done?
Lean Manufacturing is a method to reduce waste and increase efficiency using structured methods. They were created by Toyota Motor Corporation in Japan in the 1980s. The primary goal was to make products with lower costs and maintain high quality. Lean manufacturing emphasizes removing unnecessary steps from the production process. It includes five main elements: pull systems (continuous improvement), continuous improvement (just-in-time), kaizen (5S), and continuous change (continuous changes). It is a system that produces only the product the customer requests without additional work. Continuous improvement is the continuous improvement of existing processes. Just-in-time is when components and other materials are delivered at their destination in a timely manner. Kaizen stands for continuous improvement. Kaizen can be described as a process of making small improvements continuously. Finally, 5S stands for sort, set in order, shine, standardize, and sustain. These five elements can be combined to achieve the best possible results.
The Lean Production System
Six key concepts are the basis of lean production:
-
Flow is about moving material and information as near as customers can.
-
Value stream mapping - break down each stage of a process into discrete tasks and create a flowchart of the entire process;
-
Five S’s - Sorted, In Order. Shine. Standardize. And Sustain.
-
Kanban – visual signals like colored tape, stickers or other visual cues are used to keep track inventory.
-
Theory of constraints: Identify bottlenecks and use lean tools such as kanban boards to eliminate them.
-
Just-in Time - Send components and material directly to the point-of-use;
-
Continuous improvement - make incremental improvements to the process rather than overhauling it all at once.